Stainless Steel Technical Guide
Carbide Precipitation
A distinctive characteristic of austenitic stainless steels such as Types 304 or 316 is chromium carbide precipitation at grain boundaries when exposure within a temperature range of about 800-1600°F is of sufficient time duration. Less than a minute is required at 1200°F and with a carbon level of about 0.07%.
The rapid heating and cooling of the base metal in the heat-affected zone of a weld results in a zone immediately adjacent to the weld that is annealed or solution treated by the heat of welding but is cooled rapidly enough to avert carbide precipitation. However, about 1/8” away from the weld a narrow zone in which lower heating and cooling rates prevail is exposed to a temperature range of about 1200 to 1600°F for sufficient time to permit chromium carbide precipitation. The actual effective temperature range will vary with time at temperature and alloy composition. Subsequent exposure of the weldment for a sufficient time within the critical temperature range would result in “sensitizing” the whole weldment — the entirety of the weld metal and the base metal would exhibit carbide precipitation.
The propensity for carbide precipitation will vary somewhat with stainless steel grades. Nitrogen (N) alloying of base metals reduces the tendency for intergranular carbide precipitation by inhibiting carbon diffusion, thereby increasing resistance to intergranular corrosion. Whether N performs the same way in weld metals has not been documented. Molybdenum also tends to raise the tolerable level of carbon and/or heat input with respect to averting carbide precipitation.
If the “CROX” theory is accepted — that a thin film of chromium oxide provides passivity — it follows that if chromium oxide is restricted or decreased, the condition changes from more passive to less passive, with loss of some degree of stainlessness. The chromium impoverishment theory suggests that precipitation of chromium carbides around grain boundaries results in chromium-lean areas immediately adjacent to the grain boundaries, hence lack of chromium to produce a full complement of the much exalted “CROX.” This is illustrated in Figure 21.
The narrow “sensitized” zones of a weld where carbide precipitation has occurred will not be cause for concern in many industrial applications. Any Type 304 weldment will contain sensitized zones of carbide precipitation, but as long as the service environment is such that sufficient passivity is maintained, sensitivity can be tolerated. However, in unfriendly corrosive environments such as nitric acid, which become more aggressive with increased concentration and temperature, selective attack around grain boundaries (intergranular corrosion) can eventually cause physical separation of the grains and gradual removal of the sensitized base metal in the zones affected. A dramatic example of this is illustrated in Figure 22.
Sensitization (the condition of susceptibility to intergranular attack in the presence of a suitable electrolyte such as oxygenated water, water which contains chlorides, hot nitric acid, etc.) is a time-temperature-alloy composition-dependent function. Thus, for a given alloy the TIME within the critical 800-1600°F temperature range will determine the EXTENT of carbide precipitation and therefore the DEGREE of vulnerability to intergranular corrosive attack. For this reason, welding procedures — particularly for unstabilized or non-low carbon grades such as AISI 304 — should require that preheat temperatures (perhaps used for drying) be under 100°F and interpass temperatures below 350°F.
Premature failure may occur in the heat-affected zones related to specific welds, whereas the heat-affected zones related to adjacent welds on plate of the same mill heat number and filler metal of the same lot number (put in by a different welder or by the same welder except that in adjacent welds he followed acceptable procedure) may show no early evidence of weld-related attack. For unstabilized or non- low carbon grades such as AISI 304, it is particularly important to limit heat input to 30-35 kilojoules to minimize corrosive attack in unfriendly environments (aggressive solutions).
Heat Input in Kilojoules per inch = (Volts x Amperes x 60) / (Travel Speed (ipm) x 1000)
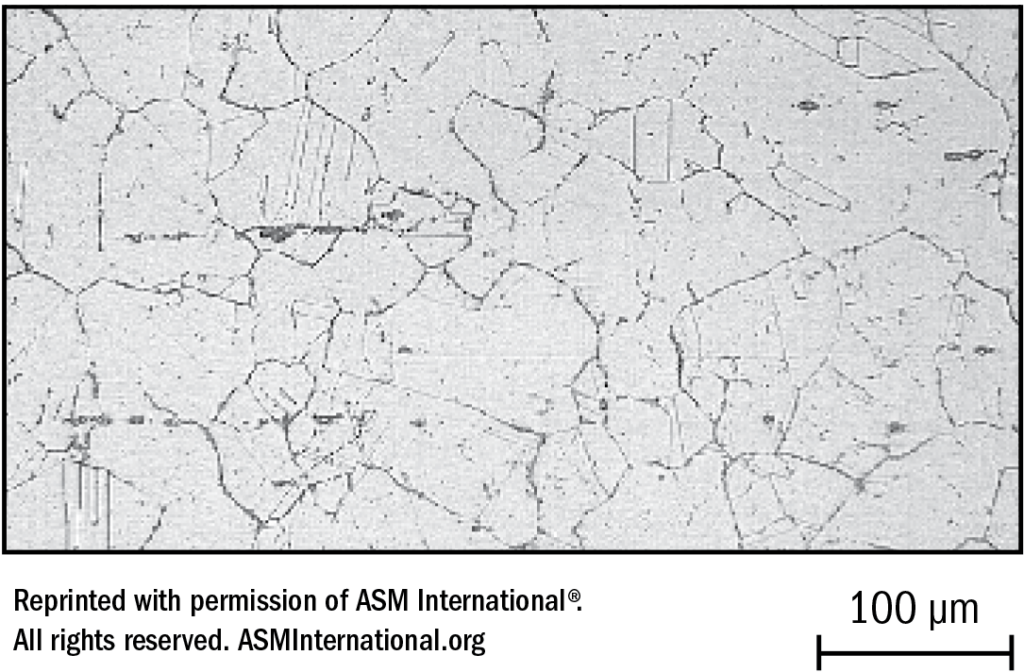
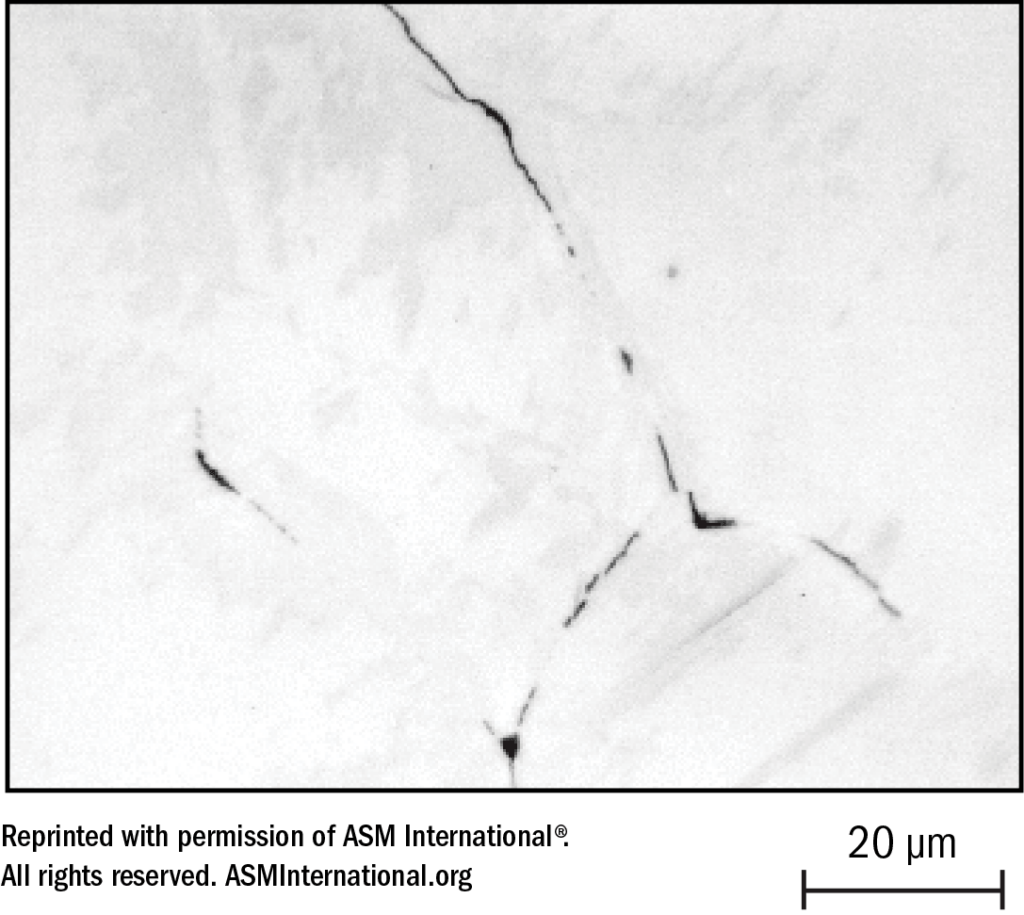
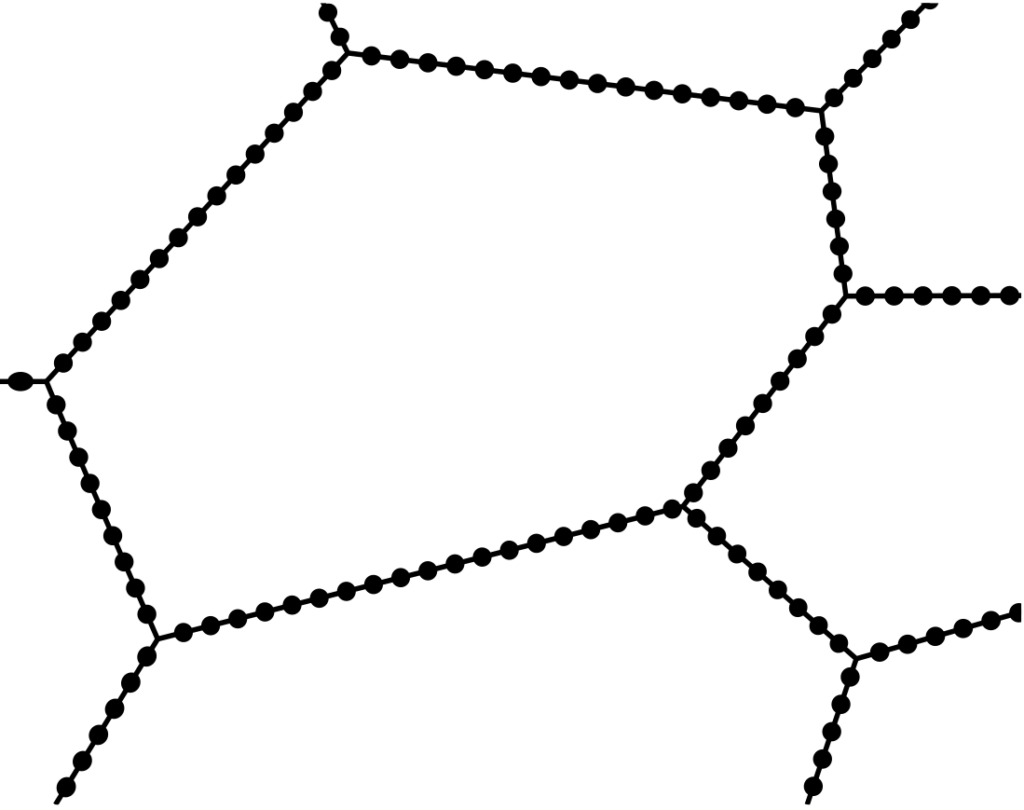
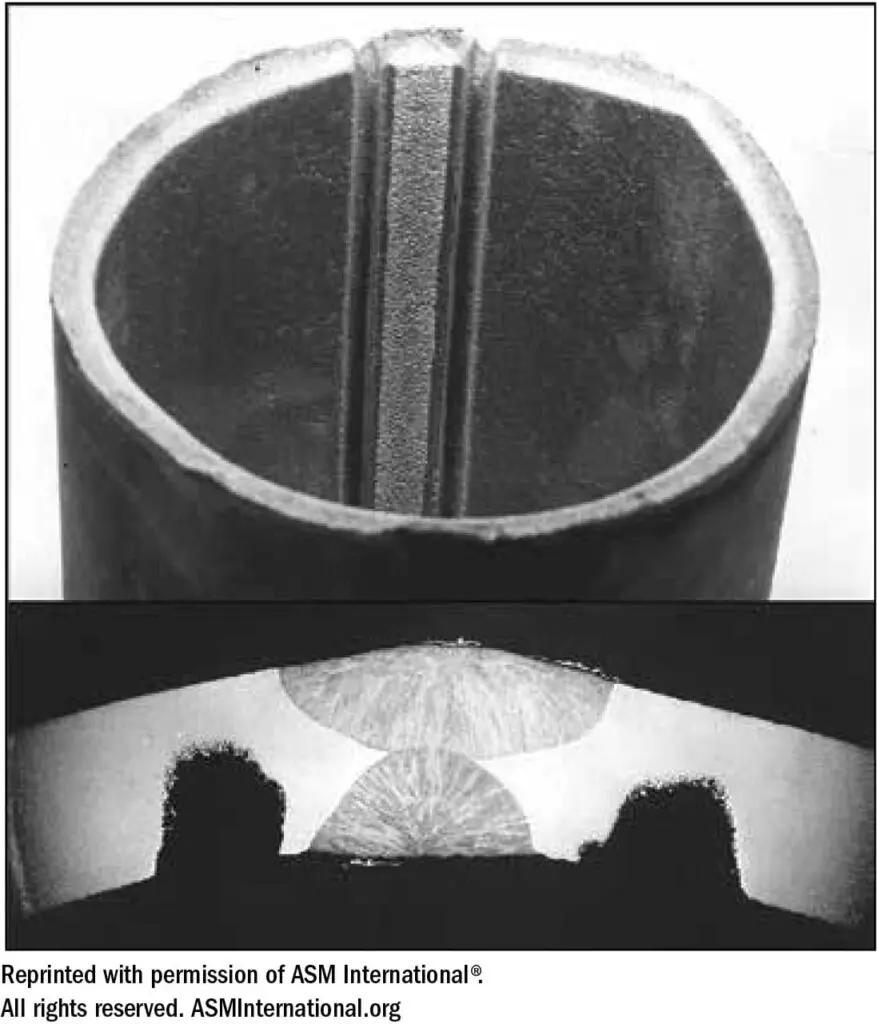
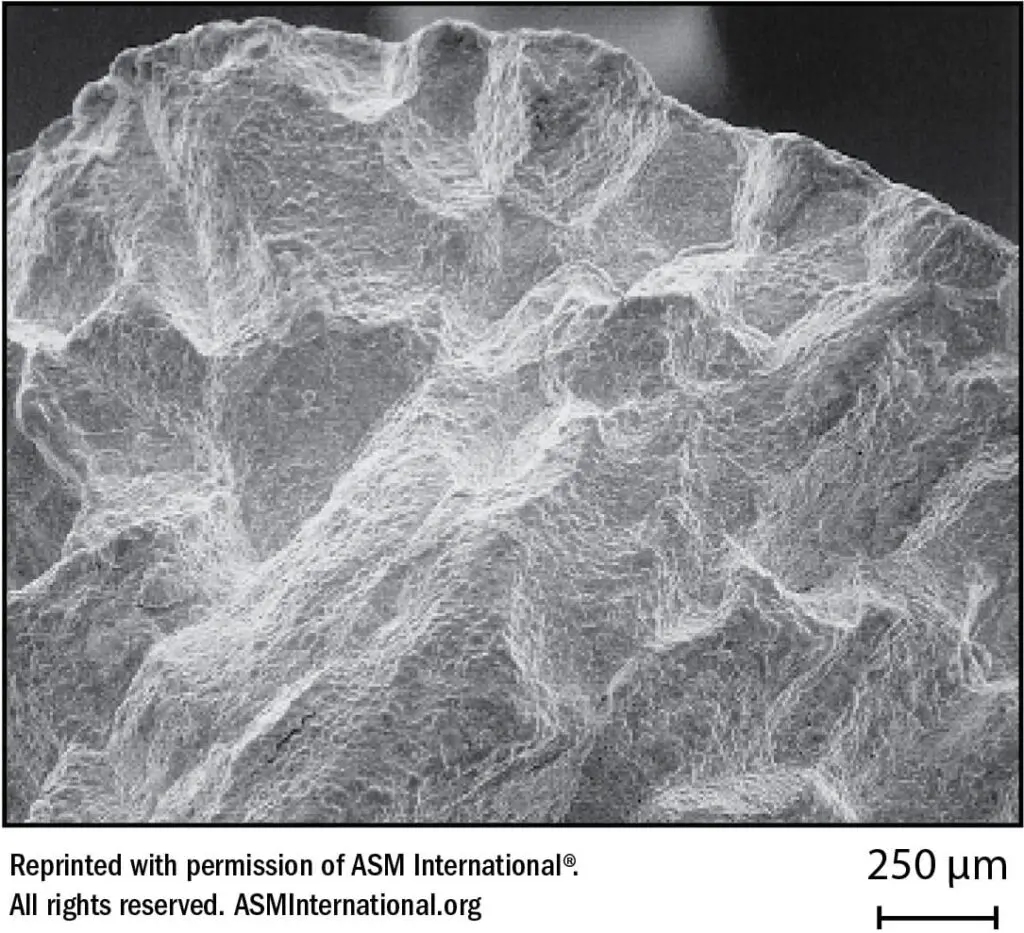
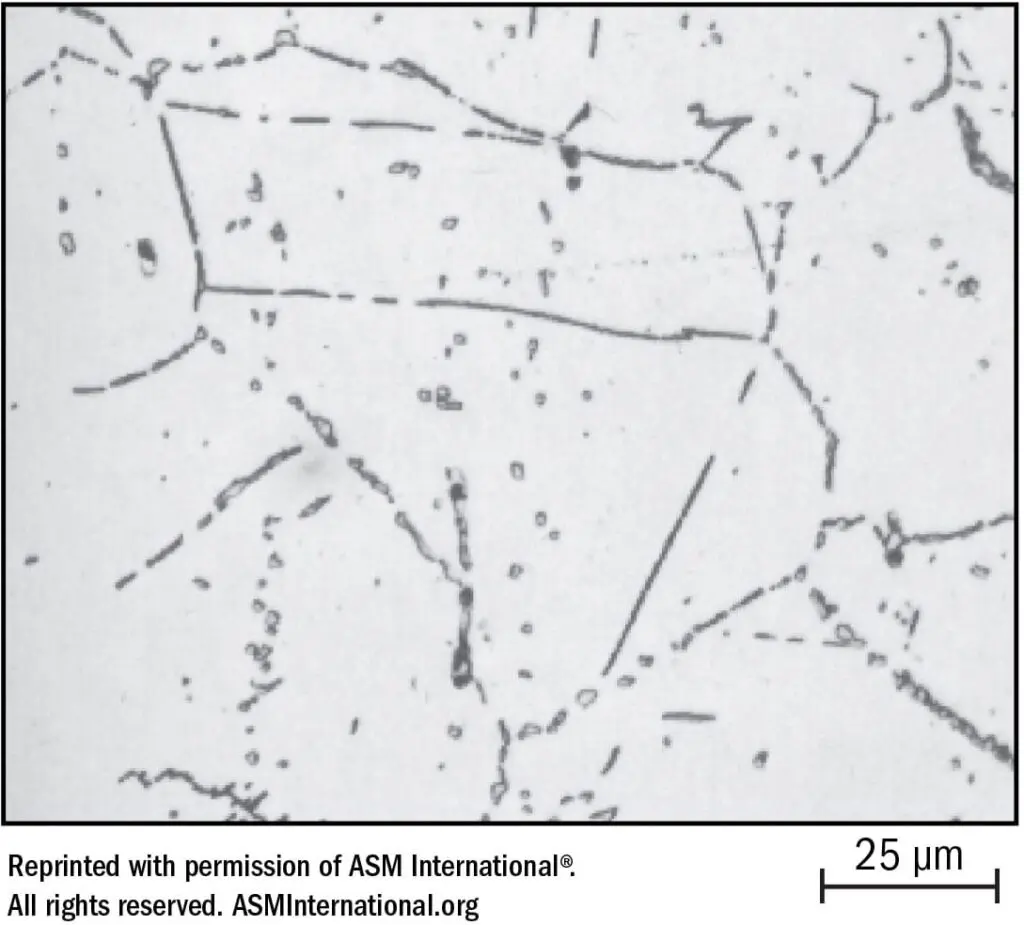
Combating Chromium Carbide Precipitation
Theoretically, if cooling in the heat-affected zone is rapid enough, carbide precipitation can be averted. Attempts to beat carbide precipitation such as wrapping the heat-affected zones in dry ice, use of chillbars, etc. are not practical and usually do not work. One way to take care of the problem is to let it happen then anneal at about 1950-2000°F (which dissolves the carbides) and quench in water, thus passing through the critical temperature range rapidly enough to avoid carbide precipitation. However, this alternative may be cumbersome and can cause distortion and excessive scaling.
There are two accepted approaches to averting carbide precipitation in austenitic stainless steels: reducing the carbon level to the point where precipitation doesn’t normally occur in welding, or doing something to prevent the formation of chromium carbides by adding niobium or titanium to tie up (stabilize) the carbon so that it does not migrate to the grain boundaries and commence the chromium carbide caper. Niobium (Nb) is the designation for the element formerly designated Columbium (Cb). Some materials, handbooks, and older publications still use Columbium (Cb). They are one and the same.
The maximum C content is 0.03% for low carbon (L) grade wrought material like AISI 304L; 0.03% for bare welding wire such as ER308L; and 0.04% for covered electrodes e.g. E308L. There is always some pick-up of C from the covering materials on stick electrodes, hence a deposit composition of 0.04% C maximum rather than 0.03% C maximum. At these low carbon levels, the heating and cooling cycle of welding provides insufficient exposure time within the sensitization temperature range to produce carbide precipitation in the heat-affected zones of the base metal.
Addition of about 0.5% to 0.75% columbium or titanium is more
than sufficient to tie up 0.04% carbon. The columbium or titanium carbides are more stable than chromium carbides and remain within the austenite matrix rather than migrating to grain boundaries. Bare wire electrodes are available in the columbium (ER347) or titanium (ER321) stabilized grades but covered electrodes are only available in the columbium grate (E347) since recovery of titanium across the arc of covered electrodes is poor.
Selection of an L or a stabilized grade will be influenced by several factors. In the first place, if the base metal is not an L or stabilized grade there is little point in worrying about the weld metal since the heat-affected zone will be sensitized anyway.
An L grade will avert excess carbide precipitation in the welded joint, but there are several applications where a stabilized grade may be preferred. Design engineers must recognize that L grades are lower in strength than stabilized grades (a fact that must be reconciled when working to the ASME Code) and that stabilized grades have higher strength at elevated temperatures. Where subsequent heat treatment or service requirements are such that exposure to the sensitizing temperature range is of long duration, some carbide precipitation of an L grade can occur. Other things being equal, during welding a stabilized grade may be slightly more crack sensitive than an L grade. Columbium is a ferritizer, which tends to reduce cracking by virtue of tendency for ferrite formation. But, at a specific ferrite level an austenitic stainless steel containing Cb may be more crack sensitive than one without Cb. Hence, the necessity exists for careful ferrite control in stabilized grades.
A weldment consisting of an “L” or stabilized base metal such as 304L or 347 and welded with 308 filler metal (unprotected from sensitization) will not exhibit sensitization within the weld metal from the first pass. However, cross-over welds would produce sensitized zones in what would then become the heat-affected zones in the first pass weld metal. For this reason, the filler metal specified for “L” or stabilized base metal should also be sensitization-resistant.
With respect to sensitization, stabilized, austenitic stainless steel base metal or filler metal in weldments does not always provide complete protection. The “belt and suspenders” approach is to specify grades containing low carbon plus a carbide stabilizer. This dual approach is common in overlay filler metals, for example, the use of 309 CbL deposited over mild steel to ensure, after dilution, a respectable 347 composition in the weld metal overlay.
Another example of the dual low carbon plus stabilized approach is specification of Type 3XX CbL base metal to avert “knife-line attack.” In weldments involving Types 347 or 321 stabilized base metals there is a very narrow zone of base metal, immediately adjacent to the weld metal, which becomes exposed to a temperature high enough to largely dissolve the columbium or titanium carbides. If, after welding, these zones are then reheated to the vicinity of 1200°F, at which temperature the solubility of carbides of Cb, Ti, and Cr is very low, chromium carbides will preferentially precipitate at grain boundaries because of the greater amount of Cr in the alloy. The very narrow “knife-line” base metal zones thereby become sensitized and susceptible to intergranular attack.
Knife-line attack can occur in some corrosive environments. It has been observed in Type 347 weldments exposed to sulphate-containing acids in refineries. Type 321 is more susceptible to knife-line sensitization than Type 347 since Ti carbides are dissolved at a lower temperature than Cb carbides, resulting in a wider sensitized zone than would occur with Type 347.
One way of avoiding knife-line attack in stabilized base metal is to reheat the joint area of the weldment to 1600°F. This produces, in the knife-line zones, selective precipitation of Cb and Ti carbides – the solubility of which is lower than that of Cr carbides. Subsequent exposure under service conditions to temperatures in the vicinity of 1200°F will not result in sensitization. If low carbon plus stabilized base metal such as Type 308 CbL is specified, the 1600°F treatment would not be required to prevent knife-line sensitization.
Within the limitations previously discussed, many weldments would be acceptable and free from carbide precipitation in the heat-affected zone where L, Cb or Ti grades are mixed or matched. That is, you could use 304L to weld 321 or 347 base metal, or 347 to weld 304L base metal etc.