Stainless Steel Technical Guide
Overlay and Clad Steel Welding – A Few Guidelines
Overlays
What you SEE is NOT what you GET where “what you see” is the filler metal composition and “what you get” is the weld deposit overlay composition resulting from dilution or the admixture of all-weld metal and parent metal. To end up with an overlay of a specified composition, the filler metal must be enriched sufficiently to reconcile dilution. With any given filler metal composition, changes in weld procedure can cause variation in dilution and, consequently, undesirable overlay composition. Therefore, to ensure consistent satisfactory results the welding procedure must be carefully controlled.
In the example in Figure 34, Type 309L filler metal at 25% dilution produces a reasonable 308 weld nugget, although C is higher than the 0.08% maximum specified for 308. A second pass, using 308L, would produce about 0.05C, 19.5Cr and 9.5Ni — a more respectable 308 composition. Substitute 1020 for the 1030 in the example and the single pass deposit with 309L would be about 0.076%C. A change in welding procedure causing a dilution increase from 25% to 40% would, in a one-pass application of 309L on 1030, result in unsatisfactory C, Cr and Ni contents.
It is often necessary to consider multiple pass overlays to assure composition enrichment. For example, if a 347 deposit over mild steel is required, the first pass could be with 309L and the second with 347; use of a special filler metal like 309L Cb might be satisfactory in one pass but C would be a little on the high side. Where a 316 composition is required over mild steel, two passes with 309L Mo would be satisfactory. Remember — welding parameters and procedure control can result in variation in dilution with consequent variation in composition. Procedure qualification should include chemical analysis on the weld nugget. There are no shortcuts.
To overcome cracking tendencies in deposits of 309L over carbon or low alloy steel base metals such as 4130, consider Type 312 for the first pass and 309L for the second pass (assuming that the service temperature is not over 800°F). Note that overlapping of weld beads minimizes dilution.
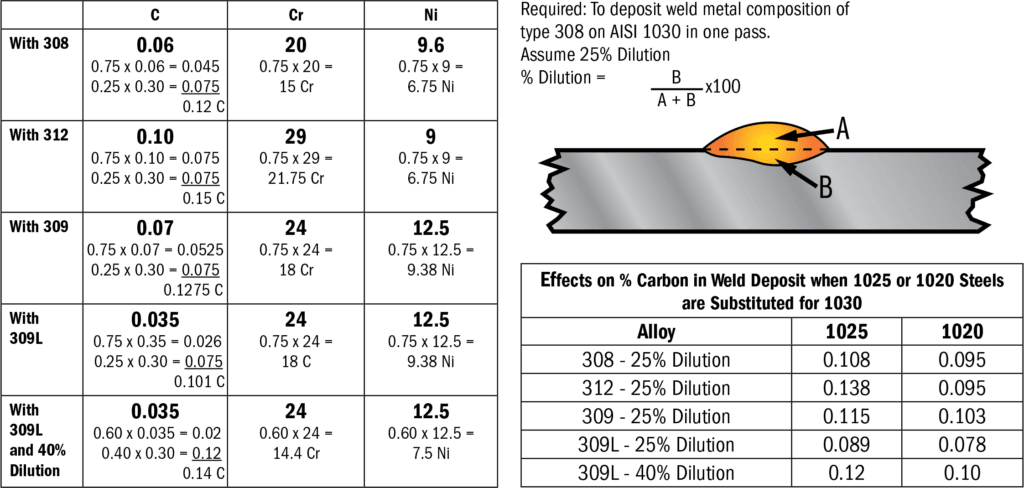
Clad Steels
When welding clad steels the dilution effects discussed in the section Overlays are of equal importance. Stainless clad carbon or low alloy steel plates are sometimes welded with stainless filler metal throughout the whole thickness, however, carbon or low alloy steel filler metal is usually used on the unclad side followed by removal of a portion of the cladding and completion of the joint with stainless.
Inexperienced fabricators should consult the manufacturer of the clad steel for detailed welding procedure and subsequent postweld heat treatment recommendations. Joining of clad steel to unclad steel sections normally requires buttering or surfacing of the clad section before joining to an unclad stainless steel section.
A typical welding procedure for stainless clad steel is shown in Figure 35. Note that Step No. 6, alternate, shows a center “annealing” bead technique for use when 400 series stainless cladding is used.
Careful consideration of filler metals is required. The unclad side requires a low carbon or low alloy filler metal of appropriate composition (XX18 for stick electrodes). For the clad side types 309L could be used for 405, 410, 430, 304 or 304L; 309Cb for 321 or 347; 310 for 310; and 309Mo for 316. Some applications may require essentially matching composition in the case of 400 series clad.
It is often necessary to consider multiple pass overlays to assure composition enrichment. For example, if a 347 deposit over mild steel is required, the first pass could be with 309L and the second with 347; use of a special filler metal like 309L Cb might be satisfactory in one pass but C would be a little on the high side. Where a 316 composition is required over mild steel, two passes with 309L Mo would be satisfactory. Remember — welding parameters and procedure control can result in variation in dilution with consequent variation in composition. Procedure qualification should include chemical analysis on the weld nugget. There are no shortcuts.
To overcome cracking tendencies in deposits of 309L over carbon or low alloy steel base metals such as 4130, consider Type 312 for the first pass and 309L for the second pass (assuming that the service temperature is not over 800°F). Note that overlapping of weld beads minimizes dilution.
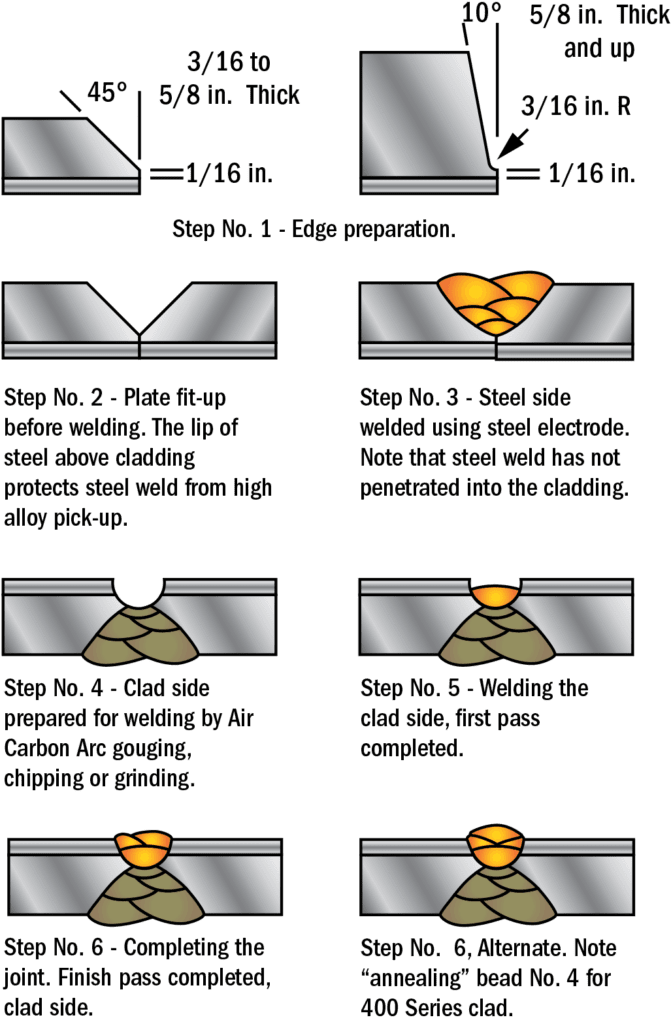