Stainless Steel Technical Guide
Class I – Martensitic Stainless Steels
The martensitic class of stainless steels shown in Figure 7 depend primarily on Cr from 11.5 to 18% as the major alloying element. This class and the ferritic stainless steel class share the AISI 400 numbering series. They are sometimes referred to as straight chromium grades. In contrast, the austenitic stainless steels are essentially chromium- nickel alloys; they are covered by the AISI 300 series for most standard compositions of wrought products. AISI 410, the principal alloy of the martensitic class, ranges 11.5 to 13.5% Cr. However, the relatively new 13Cr / 4.5Ni / .5Mo low carbon casting grade CA-6NM, provides higher strength, increased toughness, better weldability and greater corrosion resistance than the CA-15 (Type 410) casting grade.
Martensitic stainless steels exhibit magnetic properties similar to those of plain carbon steels and, therefore, are also subject to arc blow in welding. Unlike mild steels, they are air-hardening when allowed to cool rapidly from the austenitizing temperature range (1600-1850°F) where the austenite phase is predominant.
Austenitizing temperatures are reached in the heat-affected zones of weldments and subsequent cooling occurs at rates sufficient to produce martensite. In the annealed condition martensitic stainless steels have basically a ferritic microstructure with dispersed chromium carbides (See Figure 5 and Figure 6).
Carbon and chromium in the martensitic stainless steels act in concert to prevent transformation of austenite to ferrite during rapid cooling. The result is the distorted BCT structure called martensite (body- centered tetragonal — like BCC but elongated in one direction). The heat- affected zone on either side of a weldment will develop the hard, brittle martensite phase and, unless local preheating is practiced, may develop cracks due to shrinkage stresses and hydrogen. The hardness of the heat-affected zone depends primarily on the carbon content of the base metal. Increased hardness results in decreased toughness and more susceptibility to cracking. Although the most suitable preheat and interpass temperature will depend on carbon content, the mass of the joint, degree of restraint and the filler metal composition, temperatures of 400-600°F are commonly specified.
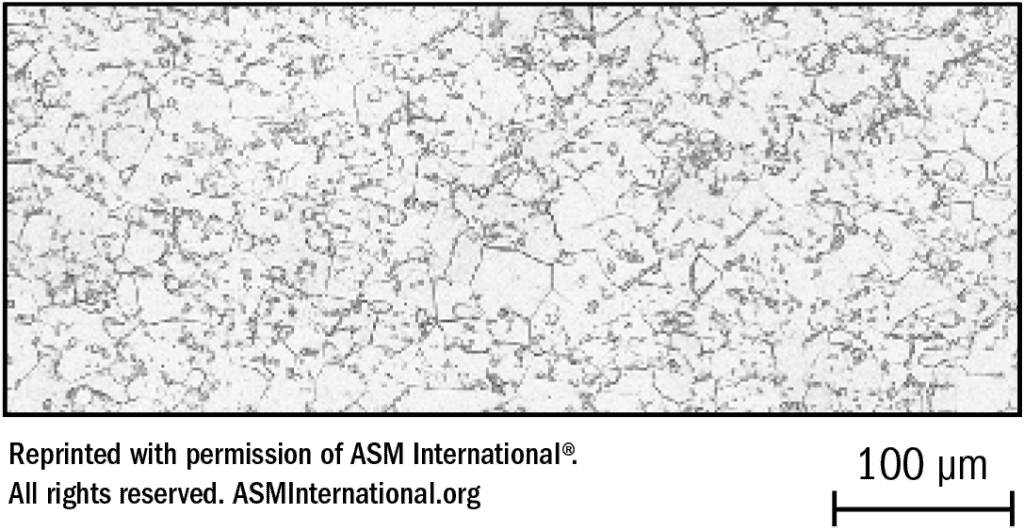
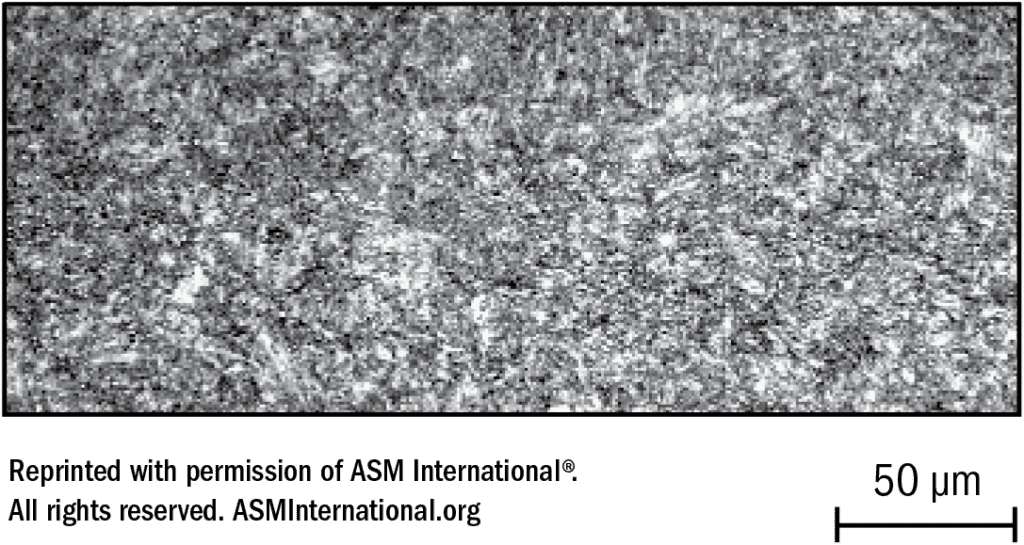
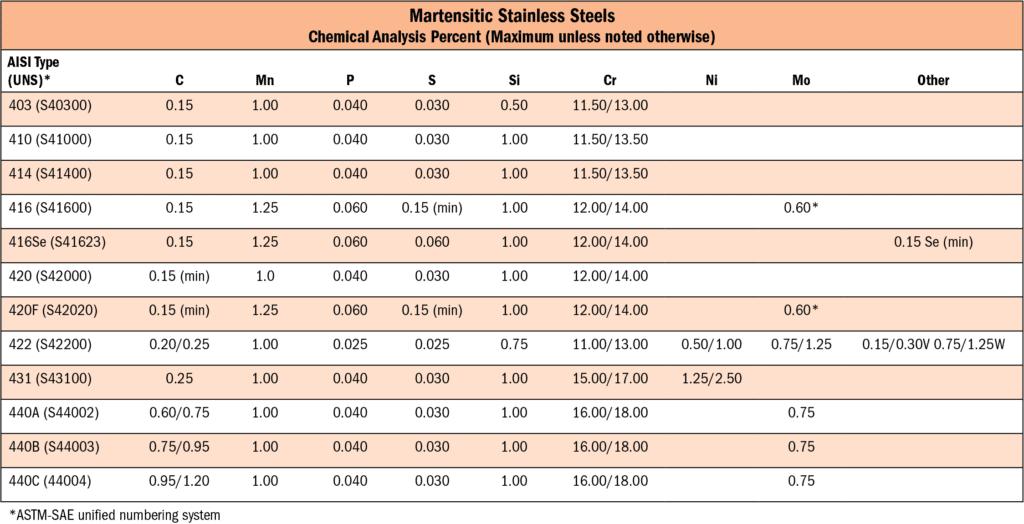
Compared with plain carbon steels, martensitic stainless steels have higher electrical resistance, lower thermal conductivity (see Figure 8) and, when rapidly cooled, brittle structure. Preheating the base metal retards the rate of cooling, permitting the weld metal and heat-affected zones to cool at a slower and more uniform rate, thereby reducing shrinkage stresses. The slower cooling also allows more of the hydrogen to escape.
Postweld heating at 1300-1400°F, followed by controlled cooling at a rate of 50°F per hour to 1100°F before air cooling, is also desirable to temper the martensitic structure in the weldment (reducing hardness and increasing ductility and corrosion resistance). Where possible, postweld heating should be done before the weldment cools down. For optimum results the weldment should not be allowed to cool below the preheating temperature between weld passes or prior to postweld heating. Where 410NiMo filler metals (somewhat less hardenable than 410) or austenitic filler metals such as 309 or 312 are used, preheating and postheating procedures may be less demanding than with 410 filler metals.
Austenitic grades are sometimes specified where the differences in composition and physical properties (such as coefficient of expansion) are acceptable for the application. If preheating or postweld heating cannot be done or is impractical, austenitic filler metals such as 309 or 312 can be specified to give more assurance that cracking will be averted.
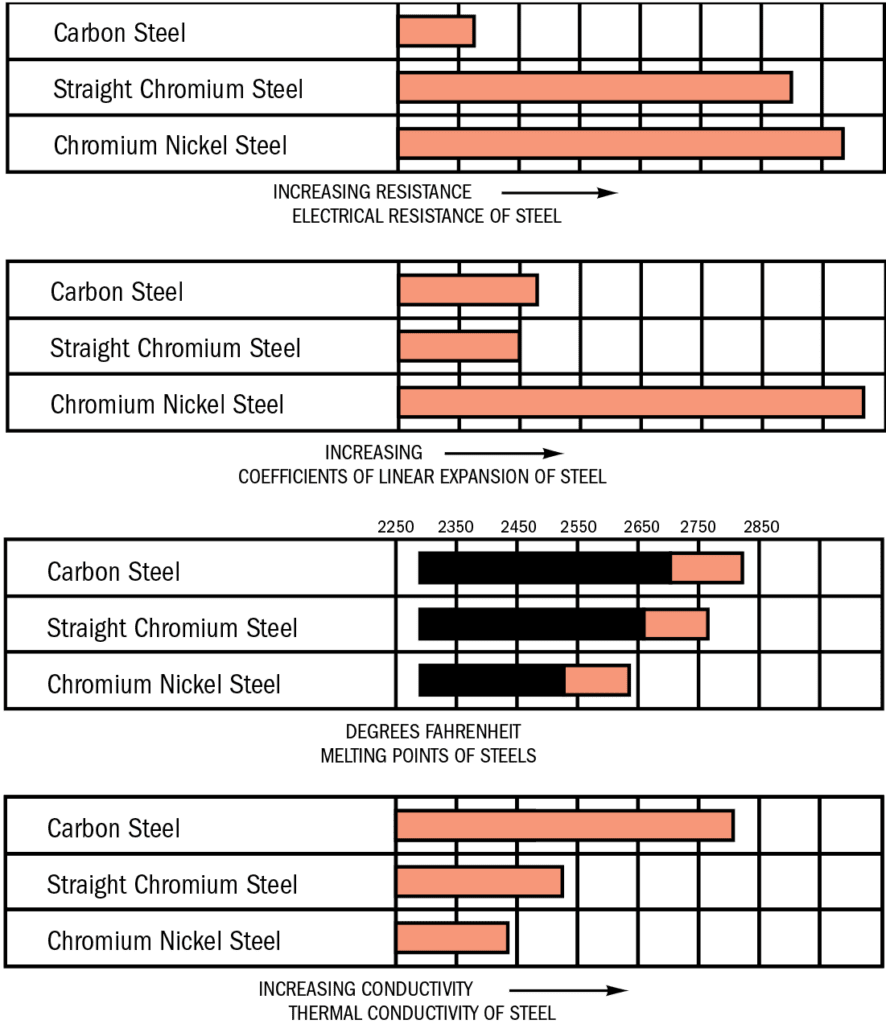
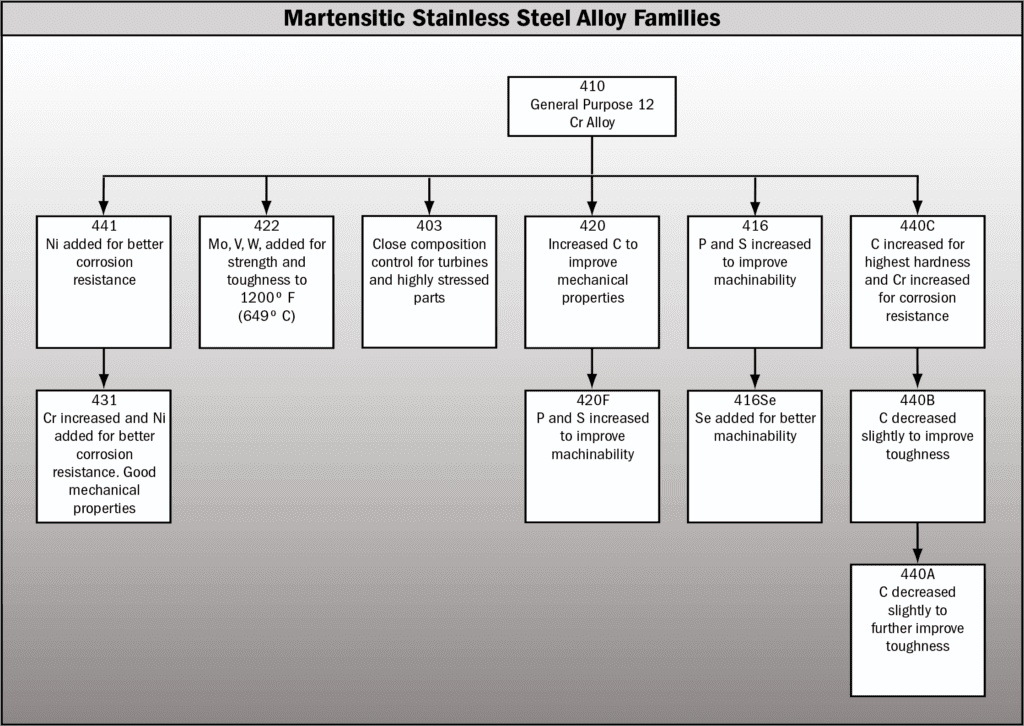
The AISI 500 series (e.g. 502 with 5 Cr, 1⁄2 Mo and 505 with 9 Cr, 1 Mo) heat-resisting steels, although not classed as stainless due to Cr being under the 11% minimum, are nevertheless martensitic and require essentially the same tender-loving care as martensitic stainless steels like 410.
Martensitic stainless steels, being lower in alloy content, are lower in cost than austenitic stainless steels. When suitably heat treated they have adequate corrosion resistance in many environments and also offer high strength and good fatigue properties together with excellent wear, oxidation resistance and erosion resistance. They are adaptable for moderately high-temperature service because of good tensile and creep strength at moderately elevated temperature. Creep strength is the slow deformation of a metal held for long periods of time at elevated temperatures under stresses which are less than the yield point.
Typical applications include Type 403 for turbine blades (high velocity fluid flow), Type 410 for valve seat facing and Types 420 and 431 for cutlery grades, razor blades and surgical instruments.