Stainless Steel Technical Guide
Corrosion of Stainless Steels – An Overview
General Comments
While general comments may be offered about the resistance of some stainless grades to corrosion (such as 316 and 320 resisting attack by sulphuric acid, and 316 and 317 resisting attack in chloride solutions) the specification of stainless steels for specific service use is not in the province of suppliers of filler metals. Selection of a stainless grade is based on a number of factors. Some of these are summarized in Figure 36. Once the grade of stainless is chosen by the fabricator upon specification of his customer or in concert with corrosion/design engineers, the filler metal producer can suggest for filler metal alloys that are matching or compatible.
Corrosion of stainless steels in unfriendly media can occur uniformly or as pitting corrosion, crevice corrosion, integranular corrosion, or stress- corrosion cracking.
Pitting Corrosion
Pitting corrosion occurs transgranularly (across the grains) when the protective oxide film (CROX) is destroyed in small localized areas. Once begun, the attack may accelerate because of differences in electrical potential between the large area of passive surface (cathode) versus the small area of the active pit (anode). Type 304 is susceptible to pitting when exposed to halide salts. Type 316 and 317, with 2-3% and 3-4% respectively of Mo, reduce pitting tendency.
Crevice Corrosion
Crevice Corrosion is a description of pitting that results from local differences in oxygen concentration associated with crevices under gaskets, lap joints, and fasteners, and also with deposits that accumulate on metal surfaces. Once begun, attack progresses rapidly. Crevice corrosion is most frequently associated with chloride environments. Mo helps to minimize crevice corrosion. Intelligent design to avoid crevices and a periodic cleaning schedule are also necessary for long range success.
Figure 36 – 200X Magnification of a Transgranular Stress- Corrosion Crack That Cuts Across Grains in Type 310 Austenitic Wrought Stainless Steel Uns Number S31000 Using an Electrolytic Etch: Oxalic Acid.
Intergranular Corrosion
This has been discussed and illustrated in the austenitic stainless steel section “Carbide Precipitation” on page 15.
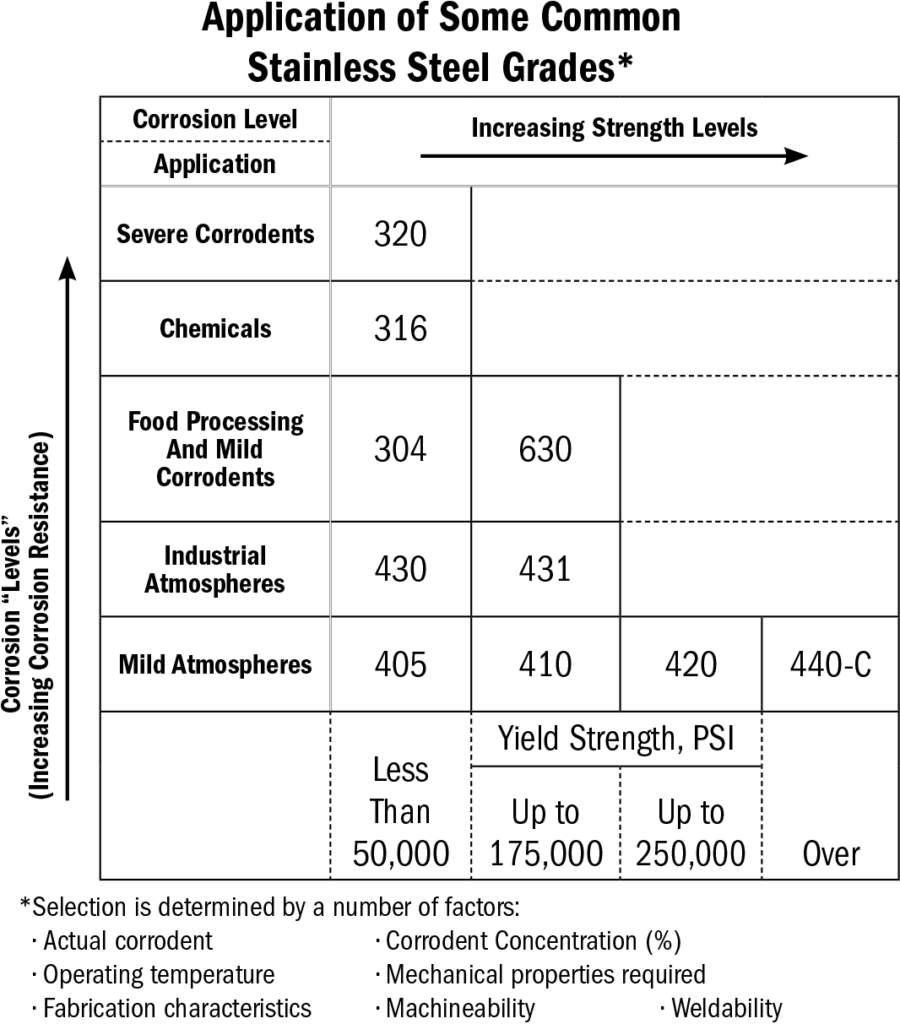
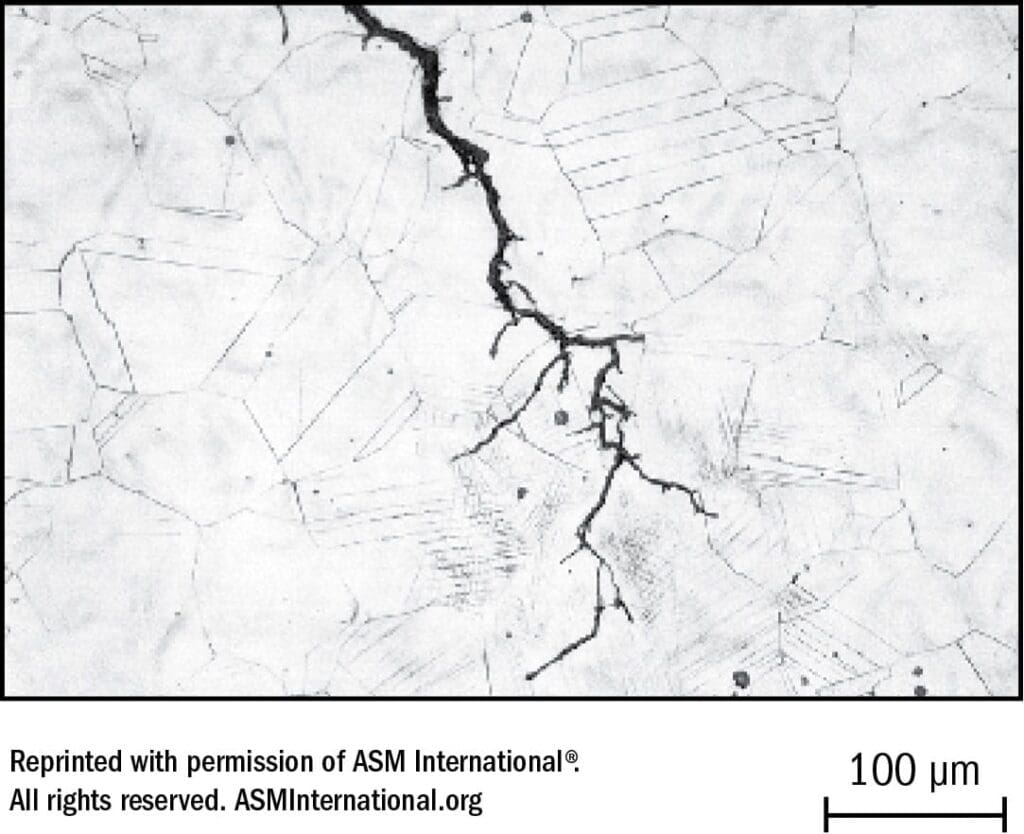
Stress-Corrosion Cracking
Stress-corrosion cracking (SCC) occurs where there is a combination of unacceptable stress together with corrosive attack in a damaging environment in the presence of oxygen and over a sufficient period of time. SCC appears primarily transgranularly. See Figure 37. Stress relieving heat treatment is often helpful in reducing susceptibility of stainless steels to SCC. For this reason stress relieving subsequent to welding should be considered.
Rusting Of 300 Series Austenitic Stainless Steels And Contamination Due To Welding
Rusting of austenitic stainless steels may be caused when a surface embedded with particles of free iron or of a surface contaminated by debris ground into the surface during storage or fabrication is exposed to moist air or water. The larger particles of embedded iron can initiate crevice corrosion.
Iron pick-up can occur from contaminated pickling solutions, grinding wheels, steel tools, welding fixtures, sandblasting operations, dust from manufacturing operations, airborne sand and iron oxide particles, particles from chipping and filing operations, and carbon steel or even 400 series stainless steel wire brushes. Only 300 series stainless steel wire brushes that are designated for use only on 300 series stainless steels should be used.
In GTAW, GMAW and FCAW processes, weld bead discoloration may occur due to contaminated shielding gases. Incursion of air through faulty equipment or poor procedure may reduce the ferrite content, making the weld deposit less resistant to cracking.
Arc strikes, weld stops, spatter, slag and heat tints can also affect the surface of stainless steel weldments.
The effect of arc strikes and weld stops can be averted by using run-out tabs at the beginning and end of a weld (where possible). Striking an arc on the weld deposit just ahead of a weld stop and then welding over the weld stop is also good practice.
Application of spatter-prevention paste on either side of the weld joint may prevent spatter from adhering tightly to the steel. Slag particles must be removed; in undercut areas they create crevices and can cause crevice corrosion.
There may be aesthetic reasons for removal of heat tint. However, the need to remove heat tint is greatest when environments are so aggressive that the stainless steel approaches the useful limits of its ability to resist corrosion. Heat tints may be removed by immersion in nitric/hydrofluoric acids, application of a pickling paste, glass bead blasting, or local electropolishing. For “how to” references see the passage on passivity on page 2.