Stainless Steel Technical Guide
How to Weld the Low Ferrite Austenitic Stainless Steels
Carefully! All phases of welding and inspection require greater attention with wholly-austenitic stainless steel filler metal grades such as 310, 320 and 330 since they are more crack sensitive than their ferrite-fortified cousins. Part of the damage can occur during cooling down from the solidification temperature to about 1800°F. Therefore, anything that will relieve stress during this period will help. Welding procedures and practice should minimize restraint. Heat input should be kept low. Keep the interpass temperature below 210°F. Thin, narrow (stringer) beads are preferred as they reduce contraction stresses (cooling occurs more rapidly during the hot-short temperature range). Weld craters should be filled and crater cracks ground out before resuming welding.
Fill the craters by holding a short arc and moving back over the finished bead before breaking the arc. Clean each bead thoroughly before welding over it.
The benefits of low heat input also are metallurgical in nature. Avoiding excessive grain growth minimizes grain boundary accumulation of low melting non-metallics that play a major role in the cause of cracking. Preheating of the heat-affected zone may increase fissures (microcracks) by a factor of 10. Low heat practice tends to minimize this phenomenon.
Since high silicon weld metal is more susceptible to cracking than low silicon weld metal, in the case of submerged arc welding, filler metal silicon content must be controlled and consideration given to possible pickup of silicon from the welding flux. Phosphorus and sulphur are major deleterious residuals that should be avoided both in plate and weld metal.
With the most crack-sensitive grades (310, 310Cb, 320, 330) it is desirable to avoid pretty beads. Smooth, flat, well-washed beads crack readily. Ugly, crowned beads are more crack-resistant. For the above grades it is important to keep the weld heating cycle as fast as possible.
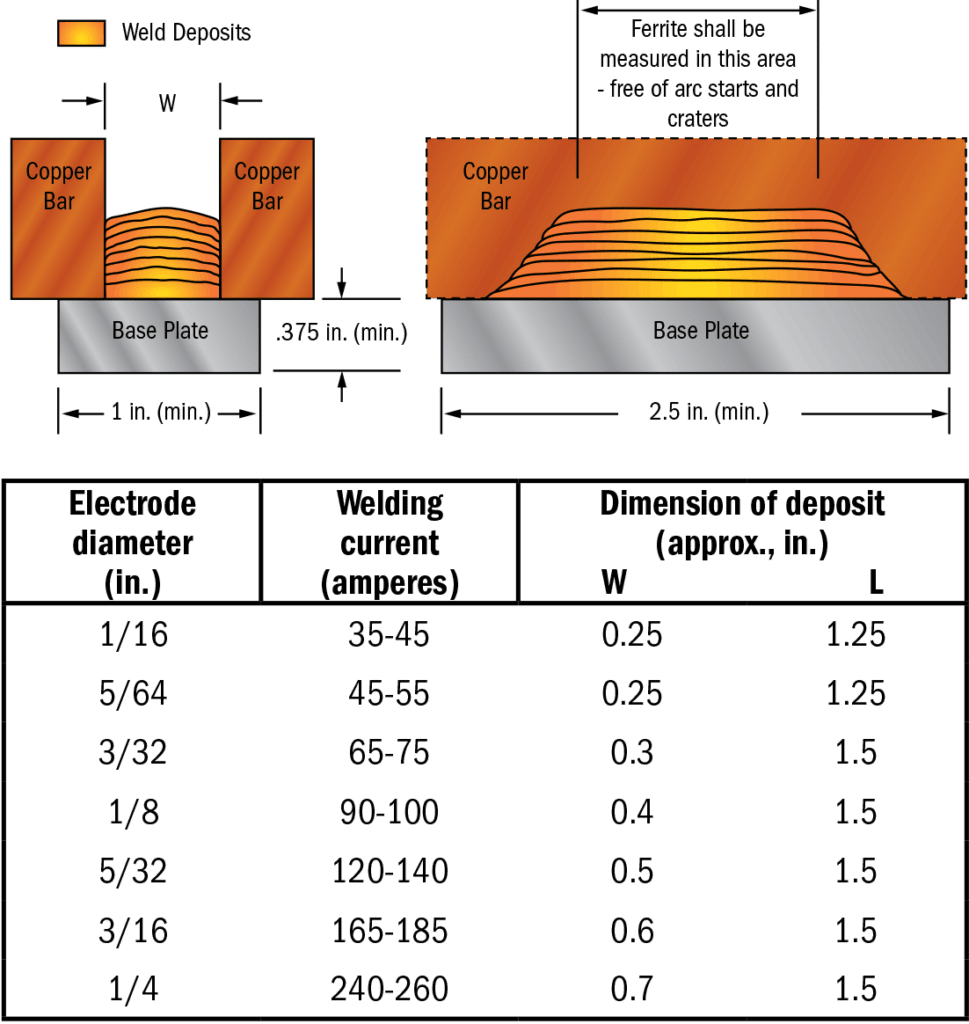
Austenitic Stainless Steel Weld Metals for Cryogenic Applications
For a detailed discussion of cryogenic toughness of weld metal deposited with stainless steel covered electrodes, request Hobart Welding Products Publication No. 1235. Cryogenic properties of austenitic weld metal deposited by covered electrodes vary widely from grade to grade. For a specific grade optimum properties may be obtained if weld metal has the following properties:
- Low in ferrite – preferably 0 FN
- Low in nitrogen – preferably less than 0.05%
- Low in carbon – preferably less than 0.04%
- XXX-15 (Lime type covering).
For service at -320°F, Type 316L filler metal is superior to Type 308L filler metal. To reduce the Ms (start of the martensite transformation) temperature to -320°F, a minimum of 10.3% Ni is required for 308L, and for 316L a minimum of 10.1% Ni. With 316L the Ni range of 11- 14% will always be above the 10.1% minimum required. With 308L (9-11% Ni) only the very narrow range of 10.3 to 11% Ni is safe; this part of the range will have very low ferrite. Furthermore, type 316L weld metal is much more crack resistant than 308L weld metal when the composition is adjusted to obtain low ferrite contents necessary for adequate lateral expansion at -320°F.