Stainless Steel Technical Guide
Precipitation Hardening (PH) Stainless Steels
What Are They?
The PH stainless steels are a family of Fe-Cr-Ni alloys with additives such as copper, molybdenum, niobium, titanium and aluminum. The principle of precipitation hardening is that a supercooled solid solution (solution annealed) changes its metallurgical structure on aging. The advantage of a PH steel is that components can be fabricated in the annealed condition and subsequently hardened (strengthened) by treatment at 900-1100°F, minimizing the problems associated with high temperature treatments. Strength levels up to 260 KSI can be achieved (exceeding the strength of martensitic stainless steels) with corrosion resistance similar to that of Type 304.
PH steels are utilized for aerospace and marine components, fuel tanks, landing gear covers, pump parts, shafting, bolts, saws, knives and flexible bellows-type joints. They fall within three general groups — martensitic PH, semi-austenitic PH, and austenitic PH stainless steels. Figure 30 lists several proprietary grades.
Martensitic PH Stainless Steels – Single Treatment
The martensitic PH group (typified b 17/4 PH, where copper is the hardener) is predominantly austenitic at the solution-annealing temperature of 1900-1950°F. Subsequent rapid cooing in air or oil results in retention of the additives such as copper and columbium etc. in solid solution at room temperature. Within the temperature range of about 300°F to room temperature there is an austenite-to-martensite transformation. Reheating of the super-saturated solid solution martensite matrix to the aging temperature of 900-1100°F triggers the precipitation of submicroscopic particles with resultant increase in hardness and strength.
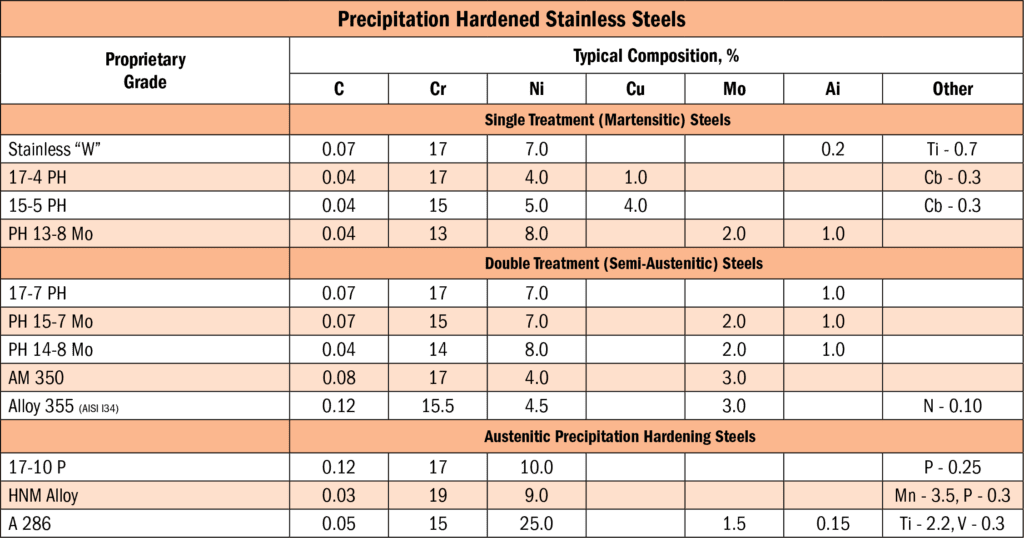
Semi-Austenitic PH Stainless Steels – Double Treatment
When cooled rapidly from the annealing temperature to room temperature the semi-austenitic PH steels (typified by 17/7 PH, where aluminum is the hardener) retain their austenitic structure — offering good toughness and ductility in cold forming operations, where martensitic PH steels would be too hard.
To produce hardening and strengthening, some transformation from austenite to martensite must first be induced to facilitate response to subsequent treatment at the aging temperature. When semi-austenitic PH steels are heated to 1200-1600°F, carbides are precipitated thereby depleting the matrix of some austenite-stabilizing elements and permitting some transformation to martensite upon cooling to room temperature.
Partial martensite transformation can also be accomplished by refrigerating below the Ms (start of martensite transformation) temperature or by cold working.
Strengthening of the semi-austenitic PH stainless steels is therefore accomplished in a two-stage or double treatment. After the initial treatment to develop martensite, the second treatment – exposure to the aging temperature of 850-1100°F — results in precipitation, hence hardening and strengthening.
Austenitic PH Stainless Steels
The austenitic group (typified by 17-10 P, where phosphorus is the additive) have alloy content such that an austenitic, non-magnetic structure is maintained after annealing and even after any aging (hardening) treatment.
When reheated to 1200-1400°F, compounds are precipitated and a lattice straining action is exerted, increasing the hardness and strength of the austenitic structure — but not to the extent achieved with the martensitic or semi-austenitic PH grades. Weldability of the austenitic PH steels is very poor due to hot shortness caused, in the case of 17-7 PH, by phosphorus-rich compounds at grain boundaries.
Welding PH Stainless Steels
The heat from welding will invariably cause solution treated or annealed base metal zones. Postweld heat treatments required to develop hardness in these zones may involve single or double heat treatments. The steel producer should be consulted, or pertinent steel producer literature referenced for recommended welding and subsequent treatment procedures for the specific PH proprietary grade involved.
Relatively thin PH stainless steels do not require preheating prior to welding. The martensitic PH grades are low in carbon and not full hardening as in martensitic stainless steels such as Type 410.
The weld metal and heat-affected zones of single pass welds will respond fairly uniformly to postweld precipitation hardening treatments. Multiple pass welds respond less uniformly, resulting in significant variations in the structure of weld metal, heat-affected zones, and base metal. Annealing after welding will provide a more uniform structure capable of responding uniformly to subsequent precipitation hardening treatments.
In welding, maintain a short arc (a long arc causes loss of chromium through oxidation) and keep the heat input low (for best ductility and toughness). Use stringer beads, avoid wide weaving, and avoid stress raisers such as sharp corners, threads, and partial penetration welds. Where possible, use starting and run-off tabs, fill craters, and grind out any crater cracks that may appear before continuing welding. When matching filler metal is not required, an austenitic stainless steel filler metal of the 309 type can be used and will provide greater ductility. The low carbon (309L) or stabilized (309Cb) versions are preferred to prevent chromium carbide precipitation if the weldment is to be postweld heat-treated in the sensitizing temperature range.
Welding of 17/4 PH plate under 4 inch in thickness can be done without preheating but interpass temperatures up to 300°F are commonly specified. With thickness of 17/4 PH plate exceeding 4 inch, preheating to 200°F and maintenance of an interpass temperature of 200-500°F is considered necessary in many applications. When welding 17/4 PH with bare ER630 wire use argon or helium gas for GTAW (TIG) welding but only argon for GMAW (MIG) welding. See section on dissimilar metal welding (Page 28) for comments on welding 15-5 PH and 17-7 PH steels with 17-4 PH (630) filler metal.