Stainless Steel Technical Guide
How Stainless Steels Work
Chromium (the key element in stainless steels) in excess of about 11 percent forms a tenacious, refractory oxide, protective film on any exposed layer, e.g., a corrosion barrier. This relatively impervious film is considered to be self-healing or self-restoring. It will, if broken, repair itself spontaneously upon re-exposure to an oxidizing agent such as air or nitric acid. Passivity, the resistance to corrosive attack under specific conditions, is enhanced by progressively increasing chromium more than 11 percent and/or by the addition of other elements such as nickel, molybdenum and copper. The degree of imperviousness of the oxide film in certain environments depends not only on the alloy composition but also on the specific medium and its concentration and temperature. While some may dispute that passivity actually results from the presence of a chromium oxide film (herein called the CROX theory), the concept does offer an exceptionally convenient working hypothesis and has been the commonly accepted explanation for more than 50 years.
Note that the term “passivation” is often used to describe a cleaning operation with nitric acid especially to dissolve iron contamination from the surface of stainless steels. References:
ASTM Standards 1985 Section I Volume 01.03.Steel – Plate, Sheet and Wire. ASTM A380 Page 196.
Carpenter Stainless Steels Working Data, Page 184 – Cleaning and Passivation of Stainless Steels – Carpenter Technology Corp., Reading, PA 19603.
Bradford Derustit Corp. – Curtis Industrial Park, Rte. 67, Ballston Spa, NY 12020. Offers liquid and paste forms of Derustit SS-3 chemical cleaner for stationery or immersible applications.
Cleaning and Descaling Stainless Steels – Nickel Development Institute, 15 Toronto St., Suite 402, Toronto Ontario, Canada M5C2E3.
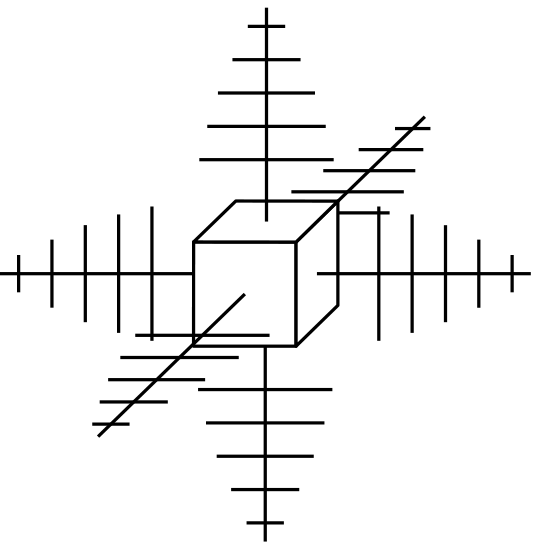
Figure 1 – Dendritic Growth of Cubic Crystal.
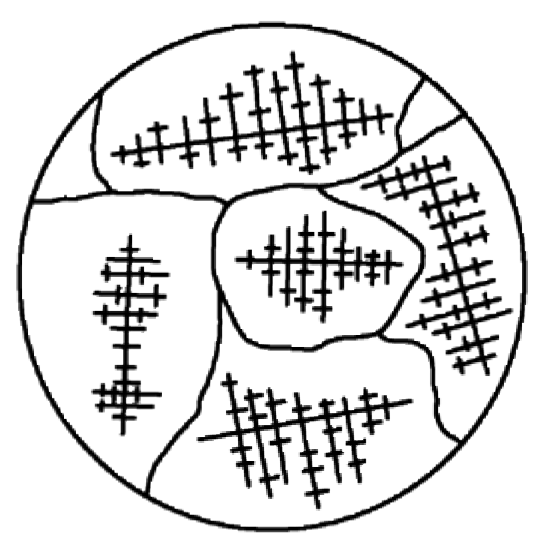
Figure 2 – Grain Size and Shape Are Determined by the Manner in Which the Branches From Dendrites Meet.
Grains and Grain Boundaries?
Before discussing the major classes of stainless steels and appropriate welding filler metals it would be prudent to review the mechanism of solidification and subsequent formation of grains and grain boundaries. When a liquid steel cools through the solidification temperature range peculiar to that particular grade of steel, the process of crystallization commences. Although individual atoms have great freedom (mobility) in the liquid state, once freezing starts they begin to orient themselves in a specific type of crystal lattice or arrangement.
Nucleation of crystals occurs simultaneously in various locations. The pattern in each location repeats itself. Crystal growth resembles pine tree formations and is described as dendritic (branching). See Figure 1 and Figure 2. During the process of solidification the separate crystals, growing at varying rates in different locations (each in their own orientation or plane of atoms), converge to form boundaries. The individual areas of uniform crystal structure are called grains and the boundary areas, grain boundaries. Grain size and shape are determined by the manner in which the branches from dendrites meet. See Figure 2.
Grain boundaries represent junctions of differently oriented crystals or regions of disarray in the atomic arrangement. The atomic structure in converging grains at random orientation cannot match perfectly at their interfaces. Therefore, between any two grains there exists a transition layer where the atoms are not in their proper places with respect to either grain. Exposure to a chemical etching solution results in preferential attack in these vulnerable grain boundary locations. Thus, the metallurgist can prepare and etch a metallographic specimen from stainless steel base metal or a weld deposit. His “crystal” ball for determining the intricacies of grain size, shape, structure etc., is called a microscope.
Subsequent to solidification, say after cooling to room temperature, grain growth – where larger grains grow at the expense of smaller ones – may occur during heating and cooling cycles. Explanation of this phenomenon lies in the realm of thermodynamics involving so-called free energy at grain interfaces. Grain growth occurs above the recrystallization temperature because grains have a tendency to decrease their surface energy. Large grains have smaller grain boundary area per unit volume, hence smaller surface energy. Because larger grains grow at the expense of smaller ones, energy is conserved.