Aluminum Welding Guide
Problem Solving – Weld Bead Contour and Penetration
The Aluminum Association deals briefly with this subject in their publication entitled, Welding Aluminum: Theory and Practice. They state that the welder learns to set the correct arc length mostly by sight and sound, which is true. But, we have expanded on this subject here in order to provide a better understanding of the science involved and to give more guidance on what the effects are of changing the voltage and amperage in the welding process.
The voltage, amperage, and travel speed selected to make a MIG weld determines the shape, size, and penetration of the weld bead. The shape, size, and penetration of the weld bead required for a specific welded component varies based on the weld joint design, section sizes of the components being welded and on the mechanical strength requirements of the finished weldment. Other considerations such as visual requirements are also to be considered. Describing the numerous physical effects of varying arc voltage and amperage during welding is best done using a chart. We have done this by assuming that the travel speed is held constant. The results shown in the chart are governed by a simple electrical formula which reads as follows:
Volts x Amps = Watts (heat)
This formula says that the total heat in the weld is the product of the volts and amps selected. Voltage controls the length of the arc. As the voltage is increased, the arc length increases. As the arc length is increased, the weld bead penetration is decreased, and the weld bead profile becomes lower and wider. With increasing arc length, droplet transfer becomes less stable at the electrode tip, expelling spatter particles from the plasma column. Amperage also has an effect on weld penetration. As the amperage is increased, the weld bead penetration is increased. In the following chart, we have listed the various welding characteristics in the left hand column and in the next two columns we show the effects of varying voltage and varying amperage. A practical application of this information is encountered when welding with the Mg based 5xxx series filler metals versus the Si based 4xxx series filler metals. Because the Mg carries less heat to the base plate than the Si in these alloys, the 5xxx filler metals are welded with a shorter arc length. For 5xxx series electrodes use a welding current in the high side of the range with an arc voltage in the lower side of the range giving a crackling sound when welding. For the 4xxx series electrodes use lower currents and higher arc voltages giving a humming sound when welding. When welding with the 1xxx and 2xxx series electrodes use the same general practice as for the 4xxx series electrodes.
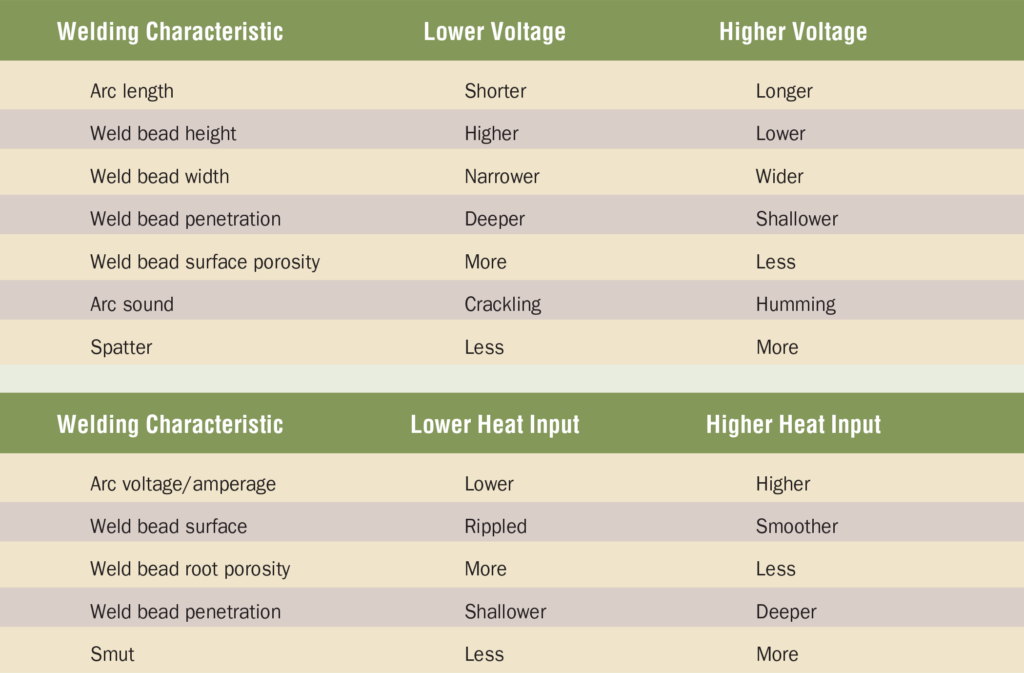