Aluminum Welding Guide
Problem Solving – How To Avoid Cracking In Aluminum Alloys
The majority of aluminum base metals can be successfully arc welded without cracking related problems, however, using the most appropriate filler alloy and conducting the welding operation with an appropriately developed and tested welding procedure is significant to success. (For information on exceptions to this statement see page 9 “Non-Weldable Aluminum Base Metals”)
The Primary Cracking Mechanism in Aluminum Welds (Hot Cracking)
Hot cracking is the cause of most cracking in aluminum weldments. Hot cracking is a high-temperature cracking mechanism and is mainly a function of how metal alloy systems solidify. There are three areas that can significantly influence the probability for hot cracking in an aluminum welded structure:
- Susceptible base material chemistry that effects the probability of cracking.
- Selection and use of the most appropriate filler metal to help prevent the formation of a crack sensitive chemistry.
- Choosing the most appropriate joint design that will provide the required dilution of filler metal and base metal in order to avoid a crack sensitive chemistry in the weld.
Hot Crack Sensitivity Curves
Aluminum crack sensitivity curve diagrams are a very helpful tool for understanding why aluminum welds crack and how the choice of filler alloy and joint design can influence crack sensitivity. The diagram shows the effects of four different alloy additions – Silicon (Si), Copper (Cu), Magnesium (Mg), and Magnesium Silicide (Mg2Si) – on the crack sensitivity of aluminum. The crack sensitivity curves reveal that with the addition of small amounts of alloying elements, the crack sensitivity becomes more severe, reaches a maximum, and then falls off to relatively low levels. After studying the crack sensitivity curves, it is easy to recognize that most of the aluminum base alloys considered unweldable autogenously (without filler alloy addition) have chemistries at or near the peaks of crack sensitivity. Additionally, the chart shows that alloys that display low cracking characteristics have chemistries well away from the crack sensitivity peaks.
Controlling Hot Crack Sensitivity in the Weld
Based on this information, it is clear that crack sensitivity of an aluminum base alloy is primarily dependent on its chemistry. Utilizing these same principals, it can be concluded that the crack sensitivity of an aluminum weld, which is generally comprised of both base alloy and filler alloy, is also dependent on its chemistry. With the knowledge of the importance of chemistry on crack sensitivity of an aluminum weld, two fundamental principles apply that can reduce the incidence for hot cracking. First, when welding base alloys that have low crack sensitivity, always use a filler alloy of similar chemistry. Second, when welding base alloys that have high crack sensitivity use a filler alloy with a different chemistry than that of the base alloy to create a weld metal chemistry that has low crack sensitivity. When considering the welding of the more commonly used 5xxx series (Al-Mg) and the 6xxx series (Al-Mg-Si) aluminum base alloys, these principles are clearly illustrated.
The 5xxx Series Alloys (Al-Mg)
The majority of the 5xxx base metals, which contain around 5% Mg, (5086, 5083) show low crack sensitivity. These base metals are easy to weld with a filler metal that has Mg content similar to the base metal. This will usually provide a weld with excellent crack resistance. These alloys should not be welded with a 4xxx series filler alloy as excessive amounts of magnesium silicide can form in the weld and produce a joint with undesirable properties. There are base alloys within the 5xxx group, such as 5052, that have a Mg content that falls very close to the crack sensitivity peak. In the case of these alloys, definitely avoid welding autogenously. The Mg base alloys like 5052 with nominal Mg contents up to 2.5%, can be welded with both the 4xxx filler alloys, such as 4043 or 4047 and the 5xxx filler alloys such as 5356.
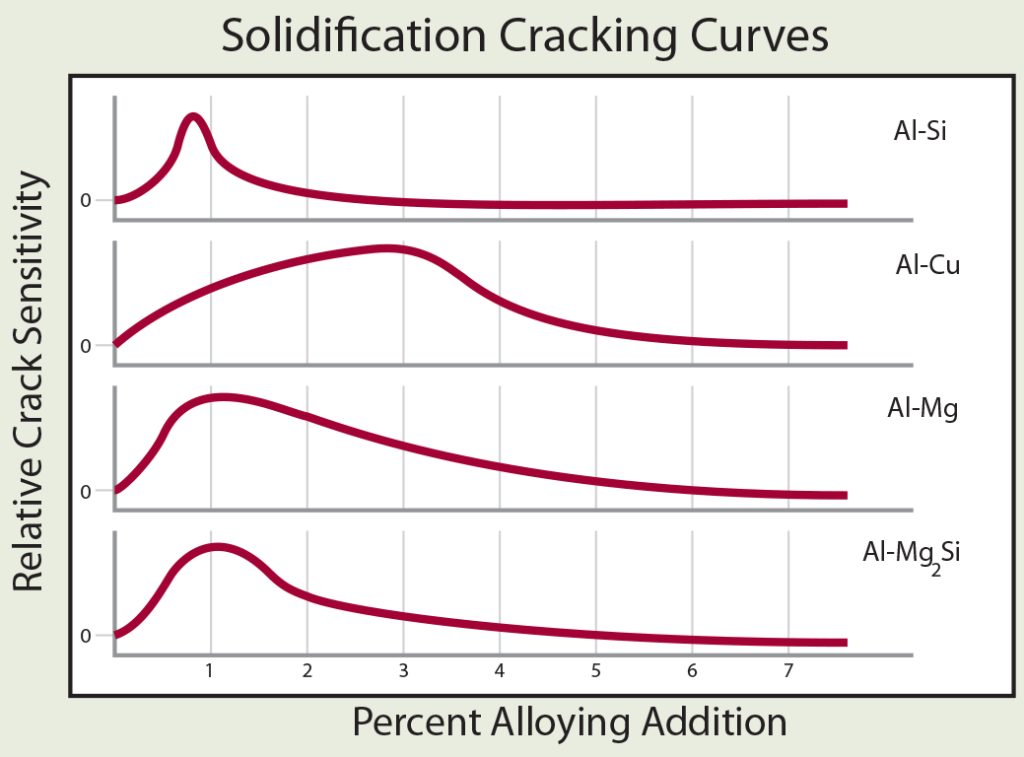
The 6xxx Series Alloys (Al-Mg-Si)
The aluminum/magnesium/silicon base alloys (6xxx series) are of a chemistry that makes them crack sensitive because the majority of these alloys contain approximately 1.0% Magnesium Silicide (Mg2Si), which falls close to the peak of the solidification crack sensitivity curve. The Mg2Si content of these materials is the primary reason there are no 6xxx series filler alloys. Using a 6xxx series filler alloy or autogenously welding would invariably produce cracking problems in the weld. During arc welding, the cracking tendency of these alloys is adjusted to acceptable levels by the dilution of the base material with excess magnesium (by use of the 5xxx series Al-Mg filler alloys) or excess silicon (by use of the 4xxx series Al-Si filler alloys). Particular care is necessary when TIG welding on thin sections of this type of material. It is often possible to produce a weld, particularly on outside corner joints, without adding filler material by melting both edges of the base material together. These types of techniques should be avoided as the absence of filler metal will produce welds that are extremely susceptible to cracking.
The Effect of Welding the 6xxx Series Base Metals without Filler Metal Addition (Autogenously)
Here we see two welds made on a 6061-T6 plate one weld with a 4043 filler alloy and one weld without any filler alloy added.
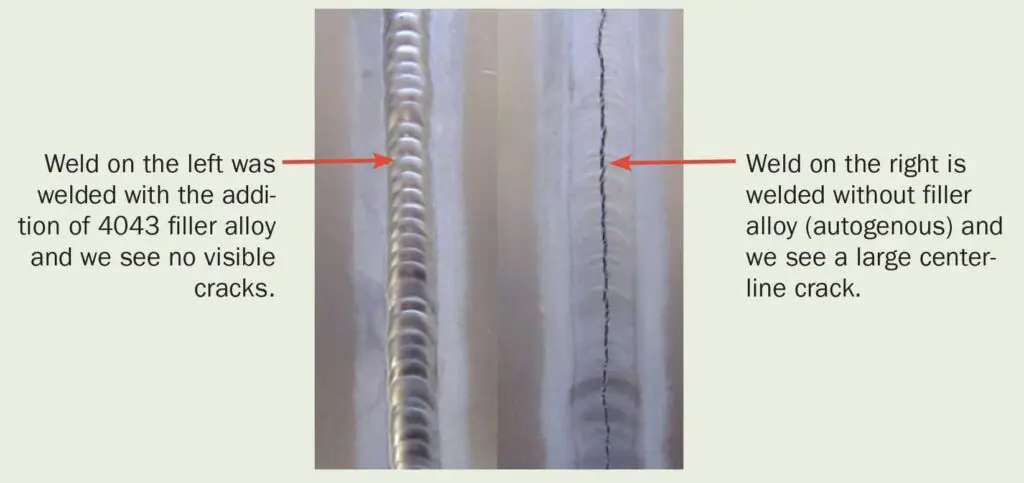
The Effect of Weld Joint Design on Hot Crack Sensitivity:
When arc welding these base metals the addition of filler metal is required in order to produce a chemistry in the weld that will create consistent crack free welds.
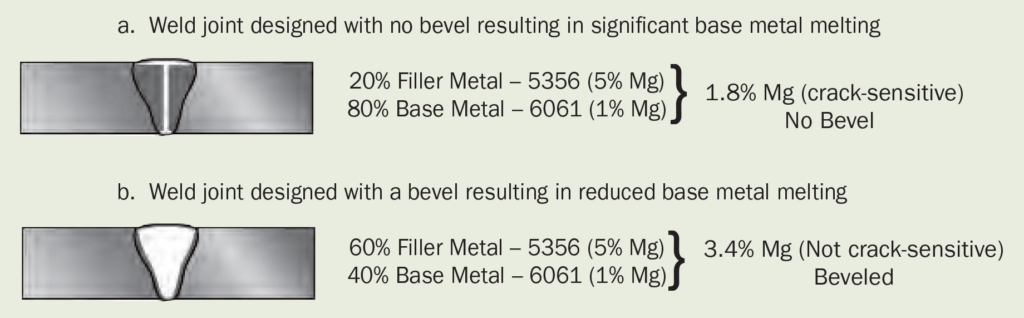
The Secondary Cracking Mechanism in Aluminum Welds (Stress Cracking)
Problem: Excessive shrinkage rates during weld solidification and further cooling.
Solution: The filler metal choice has an effect on shrinkage stress. Silicon filler metals (4xxx) have lower solidification and reduced cooling shrinkage rates than Mg filler alloys. Therefore, 4xxx filler alloys have lower shrinkage stresses and produce reduced stress cracking.
Problem: Excessive base metal melting and increased shrinkage stresses resulting from too slow a travel speed.
Solution: Increase travel speed to narrow the heat affected zone and reduce melting.
Problem: A fillet weld that is too small or concave may not withstand shrinkage stresses, and crack.
Solution: Increase fillet size and/or adjust weld profile.
Problem: A weldment that is highly restrained during the welding process may develop excessive residual stresses which may result in welding cracking.
Solution: Remove excessive restraint and/or apply a compressive force during welding.
Problem: Termination cracking at the end of the weld bead (crater cracks).
Solution: Termination cracks can be reduced by increasing travel speed at the termination of the weld, by doubling back for a short distance at the end of the weld or by re-arcing the wire several times into the puddle to add additional weld metal to the solidifying weld pool. Welding equipment with a Crater Fill feature is the best method of preventing this problem. For this reason Miller aluminum welding packages are provided with crater fill as a standard feature (see page 39 and 40).