The Right Pair: Pairing the right heat treatment and filler metal for optimized welds
Originally published in Welding Productivity
Chrome moly steels, such as 4130 and 4140, are a class of high-strength, low-alloy steels that are commonly used in elevated temperature applications and when high strength and hardness are desired. Common applications include gears, structural components, tooling and machining equipment, and transportation components, to name a few.
Part of the appeal of chrome moly steels is that through heat treatment, a variety of mechanical properties can be obtained to suit the need. Annealing, normalizing, and quenching and tempering each have their own hardness and tensile/yield strength ranges. Achieving consistent, high-quality welds requires:
- Knowledge of the pre-welded state of the base material (e.g., annealed, normalized, or quenched and tempered) and its hardness
- Use of the appropriate welding procedure, including preheat and interpass control
- Proper selection of filler material based on the post-weld application of the workpiece
Process Definitions
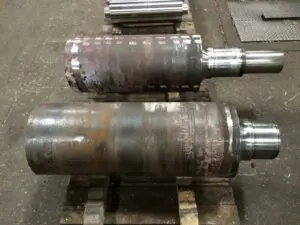
Understanding the difference between annealing, normalizing, and quenching and tempering is the first step to determining which process is best-suited for the task at hand. Annealing is the process of heating a material past transformation temperature (typically around 1600 degrees Fahrenheit in steels) and then controlling the cooling rate, usually using an oven or furnace. The purpose of this is to completely set the grain structure back to its most relaxed state.
Normalizing is similar to annealing, differing only by an air cool rather than a controlled oven cool. It still relieves stress and reduces hardness, but not quite as much as annealing.
Quenching consists of heating the material past the transformation temperature and then rapidly quenching it to achieve a more martensitic grain structure that carries a higher hardness and tensile strength. Tempering it involves heating the material back up to a given temperature and holding it there for a given time with the purpose of removing a controlled amount of the martensite that was gained in the quench.
Most codes and standards will give direction to precise temperatures and hold times. Some steels such as chrome moly 4130 and 4140 steels respond favorably to this treatment. Due to this, it is incredibly important to identify the condition of the steel before welding.
Importance of Preheating
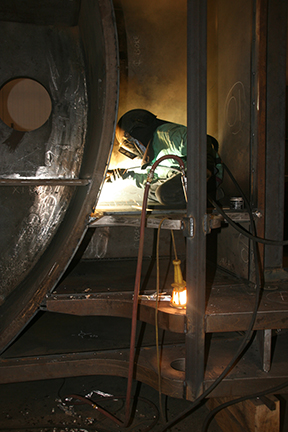
Before addressing the proper preheating temperature, the first step is to consider two components related to hardness: the hardness value itself and depth of hardness. It is typically recommended to only weld 4130 and 4140 in the annealed or normalized condition. A general rule of thumb is that anything over 25 Rc is difficult to weld, especially if it is through-hardened material. The weld could spall off and not adhere to the base material. If the weld does adhere, due to the welding operation, the desired mechanical properties in the heat-affected zone (HAZ) are lost if the base material has undergone a heat treatment.
Additionally, the hardness of 4130 and 4140 steels increases the likelihood of certain types of defects in the welds; therefore, preheating the metal is recommended to help mitigate weld failure. Preheating is essential for several reasons:
Cold crack prevention. Preheating reduces the temperature difference between the weld zone and the base metal. This is important because the base metal will act as a heat sink and rapidly draw heat away from the weld. This quenching effect can leave the weld metal and HAZ in a brittle and undesirable condition, as some hydrogen (a product that can come from moisture in the air, electrode coating, wire, flux, shielding gas or the surface of the plate) can dissolve in the molten weld metal and diffuse into the hot solid base metal along the weld boundary. If cooling is slowed due to proper preheat, the hydrogen will most likely have sufficient time to diffuse back through the weld and into the air. If cooling is rapid, hydrogen may be trapped in the HAZ in a supersaturated solution. This leads to hydrogen embrittlement and hydrogen-induced cold cracking (HICC).
Hot crack prevention. Localized heating and cooling can induce thermal stresses, which could distort or crack the welded joint. Preheating allows for both the base metal and the weld to cool at a more similar rate, which minimizes the stress put on the joint through thermal contraction and reduces the risk of hot cracking.
Microstructure maintenance. Preheating appropriately slows the rate of cooling and prevents the undesirable formation of martensite with higher carbon equivalent base metals. The minimum temperatures for preheating vary and are influenced by base material composition and thickness. When heating the base material, the preheat temperature should be established a sufficient distance from the weld joint, typically a minimum of 3 inches in all directions. Larger weldments may benefit from an even greater preheat area around the weld joint. The heat should extend throughout the entire thickness of the material. Typical base material thickness and corresponding preheat temperatures are:
- Less than 3/16 in. thick – generally no preheat needed
- 3/16 to 1/2 in. – 300 to 400 degrees F
- 1/2 to 1 in. – 400 to 500 degrees F
- Greater than 1 in. – 600 to 800 degrees F
Welding quenched and tempered steel can be challenging because it is already in a susceptible microstructure for HICC. It is generally best practice to weld the material in the annealed condition whenever possible. Situations where it would be necessary to weld on material in the quenched and tempered condition are usually in the form of repair work. It is generally a best practice to reach out to the original part manufacturer for repair procedure.
For multipass welds, it’s important that the interpass temperature remains close to the recommended preheat temperature to minimize quenching from the base metal. Checking the temperatures between passes ensures the material stays within the appropriate temperature range, mitigating premature weld failure or cracking.
Post-Weld Heat Treatment
Providing a heat treatment post-weld can help achieve specific mechanical properties and relieve stresses from the welding process. Post-weld heat treatment typically involves heating the workpiece to a specific temperature and holding it there for a certain amount of time before cooling it down gradually. Times and temperatures are determined by the desired steel properties and the welding procedure used, and it can occur several different ways.
Hydrogen bake-out or aging is an effective method to reduce the risk of hydrogen embrittlement by eliminating it from the steel’s microstructure. The process requires holding the completed weldment at a specified temperature (typically between 400 and 500 degrees Fahrenheit) and then covering or insulating the weldment. This is beneficial because it allows hydrogen to continue to diffuse from the weld metal and HAZ. The recommended time to slow cool is approximately 30 minutes to one hour per 1 inch of base material thickness.
With thicker materials, stress relieving is a common post-weld thermal treatment to relieve stress points caused from the welding process that could contribute to cracking in the weld. It requires a higher temperature — upward of 1,000 to 1,250 degrees Fahrenheit — but it should be lower than the critical point so that phase transformation doesn’t occur. Once it’s at the right temperature, the holding time needs to account for the steel’s thickness and the level of residual stresses. Cooling needs to occur gradually to allow hydrogen time to diffuse out of the weldment and prevent the reintroduction of stresses.
Typically, various codes and standards provide guidelines on the minimum required heating and cooling temperatures and rates. There are also various methods of achieving these temperatures, the most common being induction coils and ovens.
The Right Filler Metal
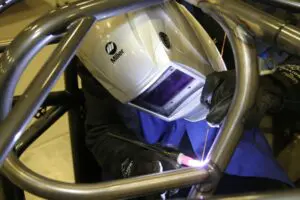
One of the most important aspects of the weld is the filler metal used at the weld joint. Choosing the right filler metal for 4130 and 4140 steels depends on several variables, such as the condition of the material prior to welding, the desired condition of the material post-weld and the design requirements of the finished product.
When choosing a filler metal, consider the yield and tensile strengths that are required for the application. It may be acceptable for the component to undermatch the strength of the base metal. Alternatively, the annealed or normalized strength might need to be matched, which can be achieved with a high-strength, low-alloy filler. If the weldment will be quenched and tempered, a chemistry match would be required for the weld to achieve the same mechanical properties as the base metal.
Filler metals that undermatch the tensile strength of the base material may improve the weld metal ductility and fatigue life. A common application where this is seen is in roll cages and tube chassis. It’s generally not recommended to choose a filler metal that overmatches the tensile strength of the base metal because it can create a loss of ductility and increase crack susceptibility in the weld.
To obtain the best results when using 4130 and 4140 steels, appropriate heat treatment and filler metal are critical considerations. It is always best practice to refer to the governing codes and standards when creating a welding procedure for your given application.