From SMAW Electrodes to Tubular Wires: Selecting Filler Metals to Weld Austenitic Stainless Steel Tube and Pipe
Known for its exceptional corrosion resistance, austenitic stainless steel (also called 300 series) has become a staple in tube and pipe applications, with 304L and 316 grades being the most prevalent. These materials’ corrosion resistance comes mainly from their chromium content (in conjunction with other elements), making them ideal to protect against exposure to the corrosive environments found in many industries (pharmaceutical, energy and chemical processing, to name a few). Austenitic stainless steel tube and pipe also help maintain safety and sanitary standards in many food-processing applications.
In addition to corrosion resistance, austenitic stainless steel offers good mechanical properties, including yield strengths ranging from 30-40 ksi and tensile strengths from 70-80 ksi. The material also provides good toughness, particularly at low temperatures.
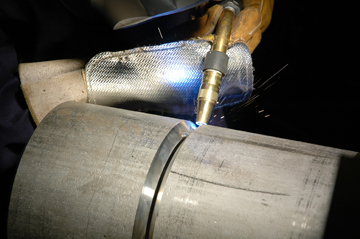
With a pulsed or advanced short circuit process, solid and
metal-cored wires can be used to weld from the root to cap
passes on thicker-walled stainless steel pipe, even out of
position.
Like any other application, welding austenitic stainless steel tube and pipe presents specific challenges. It requires special attention to heat input and post-weld cooling in order to achieve optimal results, and it also requires the right filler metal.
Why is choosing the right filler metal so important?
Hot cracking — cracks that occur immediately upon completion of the weld — are the biggest potential threat when welding austenitic stainless steel tube and pipe. This material is particularly susceptible to this defect due to its rather large grain structure.
Having the right filler metal (and controlling heat input and post-weld cooling) can help prevent cracking, as well as minimize the risk of losing corrosion resistance during the welding process.
Like filler metals for welding other materials, those for austenitic stainless steel must match the base material according to their chemical and mechanical properties. The process of making this match, however, is slightly easier with austenitic stainless steel than many other materials. The intended service condition dictates what grade of austenitic stainless will be used for the application and, in turn, the grade of material dictates what filler metal should be used. Achieving the proper chemical and mechanical properties is, thereafter, a given.
In the case of 304L austenitic stainless steel tube and pipe, the proper filler metal match is one with an American Welding Society (AWS) 308 or 308L designation, while a 316L filler metal is the appropriate choice for welding 316 austenitic stainless steels. It’s also not uncommon to have to weld austenitic stainless steel tube or pipe to carbon steel (e.g., for valves, brackets, etc.). In this case, a 309 grade filler metal should be used.
These filler metals all contain alloys that contribute to the integrity of the final weld. For example, chromium helps ensure corrosion resistance, as does molybdenum. Molybdenum also offers good high temperature performance, while nickel helps increase weld strength. The addition of silicon helps maintain weld pool fluidity and it helps stabilize the amount of austenite in the weld. That stabilization, along with the introduction of ferrite into the weld (by way of chromium and nickel) is important, since it helps refine the grain structure of the weld and make it more crack resistant.
Engineers and designers often refer to a property in stainless steels known as the ferrite number. The ferrite number is a measurement of the amount of ferrite versus austenite in the structure of the material. The ferrite number is an indication of a stainless steel weld’s ability to resist cracking, and in some cases is an indication of its corrosion resistance. The amount of ferrite present is determined largely by the chemistry of the material. In general, the goal when welding austenitic stainless steel is to reach a maximum ferrite number between 3 and 7; however, special applications may call for higher ferrite numbers to achieve the best results.
Stainless steel filler metals: the options
While filler metals with 308(L), 316 and 309L designations are appropriate for welding austenitic stainless steel tube and pipe, it’s still important to know the attributes, benefits and limitations of the specific types of filler metals within each designation. In every case — from GTAW cut lengths to tubular wires — these filler metals have their best uses, proper welding parameters and shielding gas requirements. Always check with the filler metal manufacturer for recommended usage.
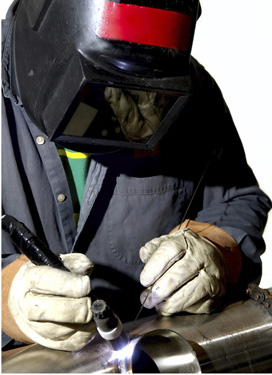
tungsten arc welding) process, which uses filler
metals called cut lengths or filler rods, is among
the most prevalent for welding thin-walled tube
and pipe.
Also remember to keep these filler metals in a clean, dry area of a similar ambient temperature as where they will be welded. Swings in temperature between the storage area and weld cell can lead to condensation, which damages the filler metal and can introduce weld defects.
GTAW cut lengths
Due to its high quality results, the GTAW (gas tungsten arc welding) process, which uses filler metals called cut lengths or filler rods, is among the most prevalent for welding thin-walled tube and pipe. These filler metals also do not produce any slag, minimizing the opportunity for slag entrapment and eliminating the need for post-weld cleaning. Cut lengths are available in a range of diameters (from 1/16 to 1/8 inches) and in industry standard lengths of 36 inches.
As a general rule, a single welding pass with a GTAW cut length as filler is adequate to complete a weld on thinner-walled tube and pipe. A GTAW root pass is also prevalent when multi-pass welding on thicker-walled pipe (particularly for high-pressure, critical applications).
One disadvantage to the use of the GTAW process, however, is its slowness. It also requires back-purging with shielding gas, which can add to costs and downtime for setup.
SMAW electrodes
SMAW (shielded metal arc welding) electrodes are frequently used for welding austenitic stainless steel tube and pipe, mostly because of their ready availability and their familiarity among welding operators. They also aid in achieving proper ferrite numbers. SMAW electrodes, however, are often considered slow and inefficient to use in comparison to other filler metals.
SMAW electrodes are only 12 inches long, so they require frequent changeover when welding. In reality, welding operators only weld to within 3 inches of the end of this filler metal before changing to a new one. The downtime for changeover and the stub loss can cost time and money.
Still, for austenitic stainless steel tube and pipe applications that are out-of-position or require access into complex joints where a welding gun cannot reach, SMAW electrodes are a good choice. These filler metals also do not require an external shielding gas, so they are portable and work well for field welding.
Stainless steel filler metals are typically available in diameters ranging from 3/32 to 5/32 inches. Some welding operators may find them to be a bit more difficult to weld with; depending on the exact SMAW electrode, the weld pool may be more or less fluid. The slag on these filler metals can also be cumbersome, since it’s a bit more fluid than that found in stainless steel flux-cored wires. In either case, the slag will require post-weld cleaning.
Solid wires
Solid wires are a very common filler metal choice for welding thicker-walled austenitic stainless steel pipe — for example, over 1/2 inch. Welding operators can use these filler metals to weld fill and cap passes in the flat or horizontal position while the pipe is being rotated (e.g., after completing a GTAW root pass). Solid wires can also be used to weld out of position for root, fill and cap passes using a pulsed or advanced short-circuit process.
It can be more difficult to alloy stainless steel filler metals to match the chemistry of austenitic stainless steel pipe, which in some cases can affect the availability of these filler metals and the size of the lots that filler metal manufacturers make. The raw materials needed to manufacture stainless steel filler metals are available in large heats and by a single chemistry. Should a company need very specific levels of an element in their wire (chromium, for example), they may have to purchase very large batches of the solid wire and it may take more time to develop.
That said, solid wires provide good deposition rates when welding on austenitic stainless steel pipe, making them a more productive choice than GTAW cut lengths or stick electrodes.
They are available in diameters ranging from 0.030 to 1/16 inches.
Metal-cored wires
Metal-cored wires are becoming an increasingly popular alternative for welding thicker-walled austenitic stainless steel pipe. They are available in 0.035- to 1/16-inch diameters.
Like solid wire, stainless steel metal-cored wire requires pulsing or advanced short-circuit processes to weld out of position, and with these processes they can be used to weld from the root to the cap. These wires, however, provide even greater productivity advantages.
Metal-cored wires typically offer faster travel speeds and greater deposition rates than solid wires. Combined, these attributes allow welding operators to place more filler metal in the weld joint faster.
Filler metal manufacturers can also alloy metal-cored wires more readily to meet specific chemistries of austenitic stainless steel and in smaller batches, decreasing the waiting period for specialty orders and reducing the amount companies need to purchase. Metal-cored wires are also very good at bridging gaps, so instances in which an austenitic stainless steel pipe may be “out of round” present less of a challenge during the welding process.
One disadvantage to stainless steel metal-cored wires is their cost. They tend to be more expensive than solid wires, but many companies find that the productivity and quality improvements outweigh the wire’s per-unit cost.
Flux-cored wires
Gas-shielded flux-cored wire is an excellent option for achieving high deposition rates when welding out of position on thick-walled austenitic stainless steel pipe. Unlike solid or metal-cored wires, this filler metal does not require a special power source to weld out of position; the flux coating on the wire acts like a dam that helps hold the molten weld pool in place. This wire is a good option for improving productivity due to these attributes.
Flux-cored wires, however, produce higher levels of smoke than other filler metals and generate a slag that welding operators will need to chip or grind in between passes and after the cap pass. These activities could lead to greater downtime for cleanup, and companies will need to consider that when assessing the overall filler metal selection.
As with any welding application, consult with a trusted welding distributor or filler metal manufacturer regarding questions about flux-cored wires or other filler metals for austenitic stainless steel tube and pipe.