Uncover the Savings Potential in Your Welding Operation
Labor is a major cost driver in most welding operations — typically comprising 85 percent of the overall costs. Many companies, however, often view labor as a fixed cost. They rarely review its productivity in the same manner that procurement departments review purchased items and are incentivized to drive cost savings through lower consumable cost. There is value, though, in reviewing productivity and determining how to reduce time spent on non-value-added activities, such as grinding, part fit-up and rework. Since these activities don’t contribute directly to throughput, they can have a significant and negative impact on the bottom line.
An assessment of the pre-weld, welding and post-weld activities can help a company uncover potential productivity improvements and cost savings in the operation.
This examination may reveal numerous steps that a company can take to drive improvements. For example, changing the welding process and filler metal may result in significant advantages.
Evaluate the process
Assessing the welding operation is the first step to uncovering potential improvements. The goal is to identify areas that can be enhanced and to look for non-value-added activities that may be hindering productivity or unnecessarily increasing costs. There are several key factors to consider.
Wire and process: What is the welding process and wire type currently being used? Are there specific reasons they were chosen and is the choice effective?
Material condition: Consider the condition of the incoming material being welded. Is it clean or does it have a finish? How is it being stored? Follow the material through the welding process, looking at how it needs to be treated to achieve a quality weld. Prior to welding, is it formed or cut? How much control is there over the part condition throughout the process? This can impact filler metal and welding process choice.
Shielding gas: How is shielding gas being supplied to the welding process in a facility? If a bulk gas system is used, it may hinder the company making a change, but shielding gas mixtures may be required for a different welding process or filler metal.
Welding process: How are the parts being welded? Different positions — such as flat, horizontal or vertical — are better suited to certain welding processes and filler metals. Is fixturing or welding automation being used? A robotic system may not be operating at its full potential if it isn’t paired with the right filler metal.
Weld finish: Is a specific weld finish a priority or necessity? If the parts will be machined later, the finish may not matter. If the parts will be painted or coated after welding, it impacts which welding process or filler metal is the best choice for the application.
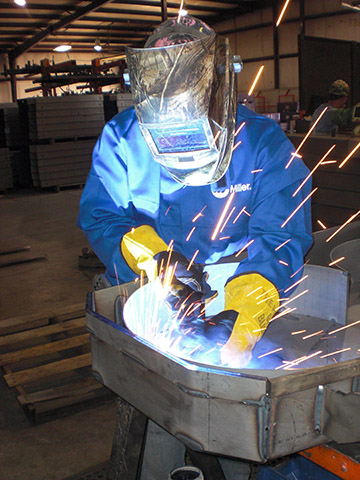
activities can help a company uncover potential
productivity improvements and cost savings in the
operation.
Understand key drivers
After assessing the welding process, it is possible to identify and prioritize the challenges or key drivers.
Note any non-value-added activities such as grinding, chipping, sandblasting or applying anti-spatter spray that are incurring time and adding costs to the operation. In the pre-weld process, determine whether part fit-up is inadequate or if it will require fixturing or clamps. If that is true, it could be due to the forming operation upstream, or due to the condition in which parts are received from an external supplier.
Evaluate how much time it takes to complete a weld. Poor part fit-up, poor part movement or indexing during the weld, or spatter that requires post-weld cleaning can all play a role in the amount of time spent on non-value-added activities — which increases costs and reduces overall arc-on time.
It’s important to establish a baseline for how time is being spent during welding. In some operations, actual arc-on time may only be 15 percent of the process time. Ultimately, an operation wants as much arc-on time as possible. Reducing the time spent on non-value-added activities is the key to achieving this.
Given the numerous factors and key drivers, consider how alternative methods such as different welding processes or filler metals could help reduce non-value-added activities to improve productivity and reduce costs in the operation.
Consider welding process and wire options
For some applications, changing the welding process or filler metal has the potential to provide significant savings. Consider some key factors to determine which process or filler metal is best suited to the operation’s needs.
Metal-cored wire: Converting to a metal-cored wire is a good option for operations that use positioners or weld in the flat and horizontal position. Because metal-cored wires deliver low spatter levels, they are good for operations that spend a lot of time on post-weld grinding or buffering to remove spatter. Metal-cored wires contain higher levels of deoxidizing elements than solid wire, making them generally better suited to welding over mill scale, and they reduce the need to apply anti-spatter compound. Also, metal-cored wires offer greater deposition and a wider penetration profile than solid wires, making them more accommodating to wider gaps and poor part fit-up.
In addition to the productivity gains an operation can see from eliminating non-value-added activities, a conversion to metal-cored wire can provide cost savings in other ways. For example, when personal protective equipment (PPE) is a high cost, switching to a metal-cored wire designed to produce low levels of manganese can help minimize the fume source, so operations can potentially save money on PPE purchases and maintenance.
Flux-cored wire: In an operation that requires high volumes of out-of-position welding, a flux-cored wire may provide a good option to improve productivity. A gas-shielded flux-cored process deposits more filler metal in vertical or overhead positions compared to metal-cored or solid wire running in a pulsed mode. Applications that require filling very deep grooves or welding on heavy steel that is several inches thick are also good options for flux-cored welding, which can quickly deposit more metal into those joints.
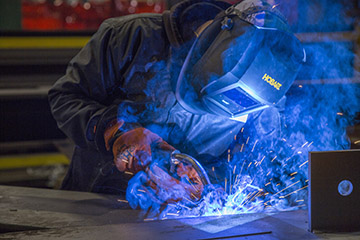
or filler metal, it’s important to follow up with monitoring and
verification to ensure the expected improvements are taking
place.
Flux-cored wires available today can operate on the same gas mixtures as metal-cored and solid wires, which makes conversion easier from a shielding gas perspective. One trade-off with flux-cored wire is that it generates more weld fumes than solid or metal-cored wires and requires the removal of slag in between passes. Another factor to consider is the deposition efficiency, which is lower than that of a solid or metal-cored wire. Some of the weight of the flux-cored wire will ultimately end up as slag that is removed and discarded.
Solid wire: If an operation does a considerable amount of short-circuit transfer welding or welding on extremely thin material, solid wire offers benefits. It’s also a good option when there are no requirements for the appearance of the final weld. Using a pulsed process also provides the ability to take solid wire out of position.
When a change is made to the welding process or filler metal, it’s important to follow up with monitoring and verification to ensure the expected improvements are taking place. Any process change or wire conversion brings a learning curve, so give the changes time to play out and re-evaluate the operation after a two- to three-month period.
In some cases, a change may require equipment acquisitions that need to be evaluated, too, as is the case with submerged arc welding or SAW. Still, for operations that weld many groove or fillet welds in the flat position, SAW might be a process to consider, since it can offer significant productivity improvements that result in a quick payback. There are solid and metal-cored wires available for the process.
Changes can yield improvements
Labor is the biggest cost in most operations, and in many cases, a large percentage of the labor is spent on non-value-added activities — costly and time-consuming work such as grinding, sandblasting and chipping.
Making a change to the welding process or filler metals can help reduce or eliminate the time spent on these costly activities.
Examining the activities in a fabrication or manufacturing application may support a change to the welding process or filler metal — and it can help ensure that the welding operation is reaching its potential for productivity and cost savings.