Tips for Welding High Strength Steel and Selecting Filler Metals
When a finished product in a welding application requires elevated levels of strength and toughness, high strength steels may be right for the job. These materials provide outstanding strength while also allowing for a reduction in material thickness — and offering less weight as an additional benefit.
While high strength steels deliver many benefits, welding these materials can present some challenges. As high strength steels become more commonly used in manufacturing and fabrication, it’s important to consider factors, such as filler metal selection, to weld these materials successfully.
The basics of high strength steels
The term “high strength steel” refers to base materials and filler metals that have high tensile and yield strengths. Yield strength is the amount of force required to deform or bend material, while tensile strength is the amount of force needed to pull or stretch a material until it breaks. Because high strength steels have higher tensile and yield strengths, they don’t flex as much under heavy loads, resulting in a lower chance of deformation or breakage compared to other steels.
High strength steels may follow an industry standard classification such as ASTM, ABS, AISI; or they may be proprietary to a steel manufacturer, in which case they will not fit traditional classification systems. For proprietary high strength alloys, the steel manufacturer can provide valuable insights into welding procedures, filler metal recommendations, and pre- and post-weld heat treatment, as well as recommended interpass temperature controls.
Due to their elevated strength-to-weight ratio, high strength steels are used to build products that carry more, weigh less and withstand extreme service conditions. In applications where it’s important to reduce weight, using high strength steel can allow for using thinner material that weighs less.
High strength materials have traditionally been required in industries, such as crane manufacturing and pressure vessels, and their use is growing in other industries like truck and trailer manufacturing.
The increased strength in these materials comes from alloying elements, primarily manganese and nickel. Some high strength steels also use molybdenum and chromium to improve strength. These alloying elements change how the steel structure forms upon cooling, making it more resistant to deformation, bending or twisting.
Using a high strength steel requires choosing a filler metal that meets the engineering design of the structure. The nature of the stresses incurred by the weldment and the engineering design of the welded structure will ultimately determine if a matching chemistry should be used.
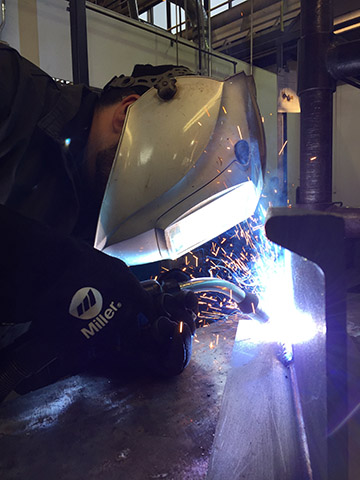
in manufacturing and fabrication, it’s important to
understand the unique considerations involved in
successfully welding these materials.
Challenges in welding high strength steels
Because of their unique properties, high strength steels can be more challenging to weld than mild steels. The material is stronger, but often used in thinner cross sections to decrease the overall weight of the structure. Because the weld metal wants to shrink as it transforms from liquid to solid during welding, the process introduces stress into the weld joint.
Reducing this stress requires close attention to several factors, including proper weld joint design, filler metal selection and heat input. Consider these common challenges when welding high strength steel:
Hydrogen embrittlement: To avoid hydrogen embrittlement and the potential cracking it can cause, use a low-hydrogen filler metal and a welding process that discourages hydrogen formation, as well as proper welding practices and joint design. These factors help reduce residual stress during the welding process, which in turn helps reduce the risk of cracking. Hydrogen induced cracking requires three elements to occur: sufficient hydrogen present in the weld metal or base metal, susceptible microstructure and high levels of restraint. Choosing a low hydrogen filler metal and welding process is crucial to reducing the amount of available hydrogen in the weld metal. Choosing proper preheat and interpass temperature control will also help control the cooling rate of the weld metal and base material to lessen the risk of cracking. Fast cooling rates are the result of a low heat input welding process, and they promote the formation of brittle microstructures in the weld metal and heat affected zones.
Risk of distortion: Compared to welding mild steel, there is a greater chance of distortion when welding high strength steel. Higher levels of residual stress present after welding, combined with thinner cross sections, can lead to distortion problems. While mild steels are often more tolerant to higher heat inputs, too much heat can threaten weld strength and integrity in high strength steels. Because high strength steels can be weakened by improper weld procedures, it’s critical to take care with heat input and joint design. In applications that require multiple welding passes, be sure to use smaller weld beads with multiple passes, rather than trying to complete a larger single-pass weld using higher heat input.
Quenched and tempered steels: Some high strength steels derive their strength from a quench and temper heat treatment. First, the material is quenched, a process by which the steel is rapidly cooled to room temperature. During the tempering process, the steel is heated to a temperature well below the melting point and helps restore some toughness. When high strength, quenched and tempered steels are welded, the heat from the arc can alter the temper on the material. For this reason, it is recommended to weld the material in the annealed condition whenever possible. Proper preheat and post-weld heat treatment are essential to minimize cracking risks.
Choosing the right filler metal
There are fewer filler metal options per material class for high strength steels. Consider the yield and tensile strength of the base material and the engineering design requirements prior to making a filler metal selection. If the base material provides 100 ksi yield strength and a matching filler metal is desired, the weld metal should provide at least 100 ksi yield strength to ensure the weld is as strong as or stronger than the base material. In some applications, American Welding Society (AWS) codes specify the filler metal type that should be used for joining specific base materials. A word of caution to not confuse yield strength (YS) with ultimate tensile strength (UTS). Often filler metals are classified by their UTS (e.g., E110C-K4).
Filler metal options with high tensile and yield strengths include low alloy metal-cored or low alloy flux-cored wires. Choosing between the types depends upon the welding process being used and what a shop is equipped to do.
Metal-cored filler metal options for welding high strength steels include AWS E90C-D2 and E110C-K4, which offer higher deposition rates and travel speeds, virtually no slag and smooth arc characteristics. Most low alloy metal-cored wires also offer excellent toughness properties and bridge gaps more efficiently than other filler metals, particularly solid wires.
Flux-cored filler metal options include AWS E81T1-Ni1C/MJ H4 and AWS E111T1-K3 MJ H8; both provide excellent low temperature toughness combined with all-position weldability. Gas-shielded low alloy flux-cored wires for welding high strength steels commonly use one of two types of slag systems: T-5 or T-1. Wires with a T-5 basic slag system usually have good mechanical properties, strength and low diffusible hydrogen levels. However, these benefits typically come at an expense; most T-5 wires are not as operator-friendly as those with a T-1 rutile slag system and create greater levels of spatter and smoke than T-1 wires. T-1 wires provide good arc stability and weldability but tend not to have as much ductility or toughness. Like any other flux-cored wires, both produce slag that will need to be removed after welding or between passes.
Just about any filler metal designed for use with high strength steel will carry a low-hydrogen designation such as H4 or H8 since reducing hydrogen is critical in many of these applications. An H4 designator, for example, signifies that the filler metal contains only 4ml of diffusible hydrogen per 100 g of weldment.
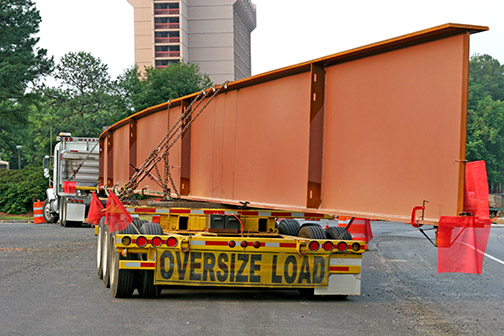
procedures can result in finished welds that are very high in strength.
These factors are an important way to minimize rework and maintain
good productivity when welding high strength steels.
Proper heat treatment
Because high strength steels can be more prone to cracking than mild steels, utilizing proper heat treatment before, during and after welding is key. In single-pass welding, heat treatment isn’t as common or may not be required, but it’s crucial in thicker, multi-pass welding applications.
Proper preheat helps maintain the right metal temperature during welding (effectively slowing the cooling rates) to prevent defects and cracking. It also helps reduce some of the residual stress that can build up during the welding process, allowing the metal to regain toughness in and around the weld joint as it cools.
The time and temperature necessary for proper preheat vary by application and are dependent on the material type and thickness.
Awareness of proper interpass temperatures is also important in multi-pass welds. Sequencing the weld process correctly helps ensure temperatures don’t exceed allowable interpass temperatures. It’s also important to check temperatures between passes to make sure the material stays within the proper range, which helps avoid premature weld failure or cracking.
Maintaining interpass temperatures also reduces changes to the grain structure of the steel during cooling, which in turn limits any mechanical changes that could adversely affect the toughness or tensile strength.
Post-weld heat treatment is sometimes necessary to ensure the welded structure cools at a uniform rate. This type of heat treatment is designed to provide ample time for hydrogen to escape the weld metal and allows the material to reduce residual stresses from the welding process.
Success with high strength steels
High strength steels offer benefits for toughness and durability in a growing number of applications, but it’s important to keep in mind several key considerations when welding these materials.
Choosing the right filler metal and using proper heat treatment and weld procedures can result in finished welds that are very high in strength. These factors are an important way to minimize rework and maintain good productivity.