Metal-Cored Wire Supports Continuous Improvement Initiatives in Full-Service Job Shop
Growing from a one room machining shop to an 180,000-square-foot facility that provides full-service fabrication, machining and welding capabilities doesn’t happen overnight. But in the case of Square Deal Machining, it happened faster than one would expect. According to general manager Carl Baatz, the company was poised for growth at the time of being purchased by the current owner, Joe Morgan, in 1998. Since then, it has expanded year over year, primarily in response to the company’s keen ability to anticipate the needs of the marketplace and its responsiveness to the demands of its heavy equipment customers. And it’s grown its customer base strictly by word of mouth.
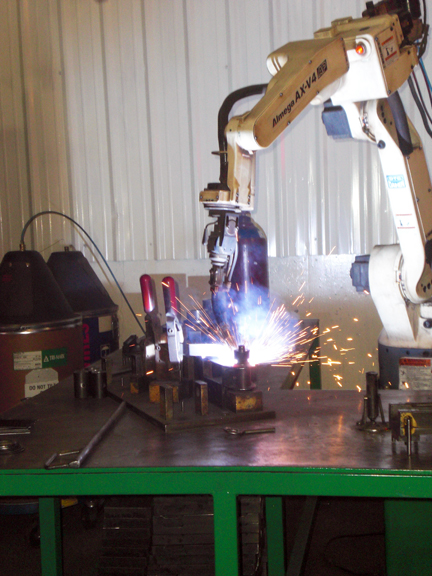
parameters on the robots at Square Deal Machining,
making it easier to weld a wide range of material
thickness with minimal adjustments.
Located in upstate New York, the company is committed to sustaining its growth and better serving its customers by regularly investing in both its employees and its equipment. From training welding operators in-house and seeking out grants for education courses, to researching and purchasing the latest technologies, Square Deal Machining continually finds ways to make its operations run more efficiently. The company focuses on carbon steel work, citing it as the best niche for its capabilities, and engages its employees in initiatives designed to make its operations more flexible and more capable of producing quality products.
“We’ve gotten to the point of such versatility here that there really isn’t anything we can’t do with a piece of metal,” explains Baatz. “Apart from the finishing, we do it all.”
In order to support the company’s continuous improvement goals, Baatz and the employees at Square Deal Machining have become actively involved in implementing quick response manufacturing (QRM) initiatives in recent years. The manual and robotic welding cells it maintains have especially benefited from the strategy. In addition to reorganizing welding cells and employing ongoing maintenance routines for equipment, the company has also replaced its solid welding wire with metal-cored wire as part of its QRM initiatives.
First alerted to the benefits of metal-cored wire technology by a customer, Baatz contacted his distributor, Tom Caminiti, owner of Endweld Supply Corp. in Johnson City, N.Y., to trial Hobart® FabCOR® 86R metal-cored wire (formerly Tri-Mark® Metalloy® 76) on the company’s manual cells. According to Baatz, the results were significant enough to implement the wire in the majority of the company’s manual cells and also its six robotic cells; a decision that has resulted in measurable productivity increases, quality improvements and cost reductions.
Refining operations for continuous improvement
Adhering to QRM principles, Square Deal Machining carefully forecasts every aspect of its business — from material purchasing to manpower — according to its customers’ estimated demands, typically forecasting three weeks in advance. Baatz says it also involves its employees with brainstorming new ideas to improve operations.
“We work one department at a time and have stand-up meetings to talk about changes that need to be made throughout our facility,” says Baatz. “The results have been tremendous. I think our busyness has come from what we’ve been able to do as a team to make this company leaner.”
Specifically, Square Deal Machining has been able to incorporate shorter lead times and learn how to operate the business at a lower capacity (typically, 60 to 80 percent), which acts as a fail-safe against unexpected demand. It also allows time for preventive maintenance and upgrades to the facility, all while keeping the company productive and profitable.
“It’s important to us to stay as lean as we can,” explains Baatz. “If we run our shop at 100 percent capacity and have an unexpected request from a customer, we’d end up with late parts. We could easily lose a customer that way.”
Because the company is also on constant deadline, it has come to rely on another important facet of QRM: reducing non-value-added activities — tasks that don’t contribute directly to the company’s throughput.
Three years ago, Morgan challenged Baatz to reduce the post-weld grinding portion of the company’s welding operations (a major non-value-added activity) and with it, the cost for purchasing grinding wheels. Recalling his discussion with a customer about metal-cored wire and its benefits, Baatz decided to try the technology as a means to address this challenge and keep improving the company’s operations. It worked, and then some.
Justifying and implementing metal-cored wires
According to Baatz, the first step in trialing Square Deal Machining’s welding operations with metal-cored wire involved a time study of the product in the manual welding cells. Because metal-cored wire costs slightly more per pound, he explains, it was critical that the company have a firm grasp on how the product could improve its welding operations in order to justify the conversion. They compared the results after the trial to the solid wire they had been using.
“We had to substantiate cost value versus time,” explains Baatz. “We knew if we could find the cost value for the company that it’d be worth it.”
By working with Hobart Brothers and Caminiti to trial and test the wire, Baatz quickly realized the value of the metal-cored technology. Not only did the trial show the potential for faster welding, but it also produced welds with less spatter than the solid wire the company was using previously, thereby reducing the need for post-weld grinding, as Morgan had requested.
The reason? Metal-cored wire’s unique physical and chemical attributes. Metal-cored uses the spray transfer process, which deposits tiny filler metal droplets in the weld puddle and generates little to no spatter.
It also offers other benefits that Baatz saw right away. Because metal-cored wire consists of a hollow metal sheath filled with metallic powders, alloys and arc stabilizers, the current travels through the outside metal sheath. The result is a broad, cone-shaped arc that provides companies like Square Deal Machining with a wider penetration profile compared to the more finger-like penetration of solid wire. This arc shape also creates a wide, consistent bead profile that bridges gaps easily and accurately without burn-through.
“We liked how broad the weld bead was [is],” Baatz says. “It gives us good weld penetration, which helps our welders, especially new ones, make quality welds with proper fusion.”
Caminiti adds, “We all really thought metal-cored wire was a good way for Square Deal Machining to keep improving itself. We were confident it would provide Carl and his team with the quality they needed and make it easier to train his welders on the manual side of the operation.”
The trial of the wire also showed that it could provide the company with greater travel speeds and higher deposition rates.
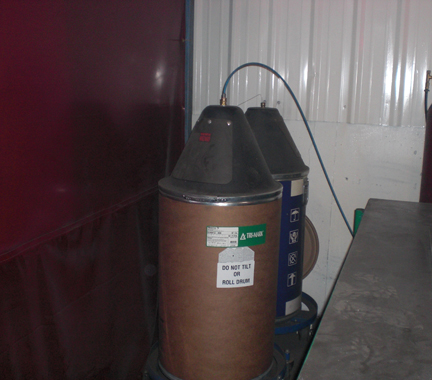
Square Deal Machining has reduced its costs by
approximately 20 percent and has improved
productivity by 30 to 40 percent.
Combined, the benefits Square Deal Machining saw during the manual welding trial justified a conversion to Baatz and Morgan. The process of changing many of the remaining manual cells, along with the robotic welding cells, began.
Converting the robotic welding cells to metal-cored wire involved bringing [former] Hobart Brothers senior welding engineer Mike Spodar into the process. Spodar took actual components from Square Deal Machining back to the labs at Hobart Brothers and developed robotic welding programs for them using the FabCOR 86R wire. Since then, Baatz, who has a background in welding and oversees all of the robotic programming, says he needs only to make minor adjustments to those programs in order to weld the wide variety of parts that the company produces.
“Hobart Brothers really showed us how wide of an envelope this product has. We wouldn’t have thought of using it on some of the lighter materials that we fabricate here,” he adds. “Now we can basically use the same programs on our robots since we have a good baseline. Our welding parameters don’t change much unless one of our parts changes significantly.”
According to Baatz, the company welds materials as thin as 16 gauge and as thick as 1 inch. The basic setup for his robots consists of operating the FabCOR 86R wire at approximately 24 volts and 180 to 185 amps and at a wire feed speed of around 300 inches per minute (IPM). All jobs are done in-position through fixturing and require strict adherence to code, mostly American Welding Society (AWS) D1.1.
Better paybacks with metal-cored wire
Since converting to metal-cored wire, Square Deal Machining has enjoyed other benefits, too. Baatz cites a cost savings of approximately 20 percent, which has come in the form of faster weld speeds, some up to 60 percent faster, and a reduction in parts rejects, particularly less instances of deformation of the steel and warping. But the most significant savings comes from having cleaner welds. Baatz says the company, as Morgan wished, has significantly reduced the need to purchase abrasives such as wire wheels and sanding disks to clean up spatter after welding. They have also been able to reallocate labor that was previously responsible for post-weld cleanup to other parts of the company in order to support the company’s throughput.
“I used to have four or five people on a bench dedicated to cleaning parts after they came out of the weld cell,” Baatz says. “Now I have two people managing the job for the same amount of product. We just don’t have the cleanup like before.”
Square Deal Machining has been able to standardize its inventory, too, and only keeps two wires in stock: FabCOR 86R and one solid wire for the very light, thin materials that aren’t suited to metal-cored wire. It has also been able to standardize on .045-inch wire FabCOR 86R wire for all of its robotic applications.
Baatz also says the company is pleased with the overall productivity increases that have resulted from converting to metal-cored wire three years ago. By Baatz’s calculations, the company has improved its productivity by 30 to 40 percent, as a result of having faster, cleaner welds.
“We’re pleased with these results, and glad that we had customers who were willing to share information about the metal-cored wire technology,” says Baatz. “Sometimes it’s hard to make changes, but for us it’s all about continuous improvement. It’s what makes us successful.”