Lambeau Field Expansion Highlights Productivity Benefits of Flux-Cored Welding in Structural Steel Applications
Baseball has Fenway Park and Wrigley Field, golf has Augusta National, and pro football has Lambeau Field. Few sporting venues in the history of the world conjure up the awe and reverence as the outdoor stadium situated in the NFL’s smallest community: Green Bay, Wis. Considered hallowed ground to one of the sport’s most avid fan bases, Lambeau Field is a national landmark that brings visitors and sightseers to the area year-round. Every fall and winter, it becomes the center of the universe for a fan base that stretches to every corner of the United States and beyond.
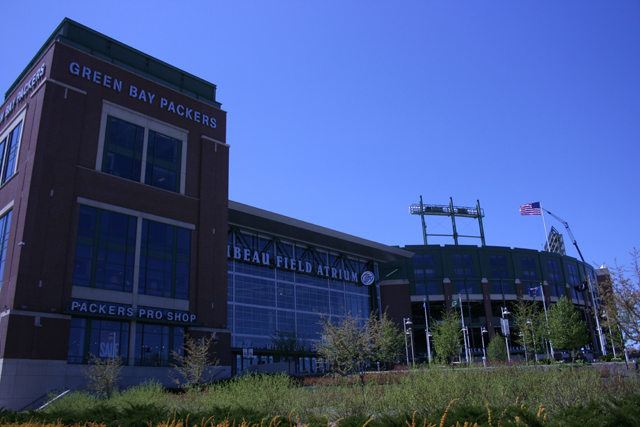
has become one of the most revered stadiums in the NFL.
In the fall of 2011, the Green Bay Packers began an expansion project to increase the stadium’s seating capacity and to improve the overall fan experience. This includes approximately 6,700 new seats in the South End Zone, a new viewing deck atop the North End Zone, enhanced entryways and stadium access, and two giant new video boards in both end zones. Stadium construction is expected to provide an economic boon to the region, creating more than 1,600 jobs over a two-year period — and the added capacity is expected to bring in an additional $11 million annually in new spending to Brown County, Wis.
The construction manager for the project is Miron Construction Co., Inc., of Neenah, Wis., with Hammes Company Sports Development, Inc., of Madison, Wis. serving as project manager. Elkus Manfredi is the project’s design architect.
As the project began, Miron Construction partnered with another Wisconsin company — Miller Electric Mfg. Co. — to bring the latest in welding technologies for the construction industry to the project. This partnership echoed a larger theme on the project, which was to put as much local talent, materials and skill into the construction of Lambeau Field as possible to highlight the capabilities of regional businesses. The partnership between Miller and Miron Construction included the addition of induction heating technology, new dual-operator welding equipment, welding safety equipment, mobile fume extraction equipment for indoor work, and the latest in self-shielded flux-cored arc welding (FCAW-S) technology. In this article, we’ll specifically look at the welding demands on the site and how Miron Construction and the ironworkers were able to use self-shielded flux-cored arc welding to increase productivity (more filler metal faster) and ensure a more efficient use of the filler metal compared to the welding process still used most frequently in the construction industry: shielded metal arc welding (SMAW, or Stick).
Steel Reinforcements Call for Extensive Welding
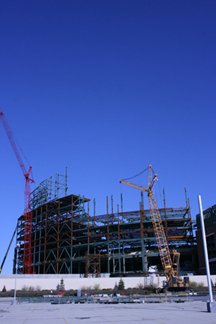
progress in early 2012.
Miron Construction began work on reinforcing existing steel structures at Lambeau Field in September 2011. Work ramped up in January as the regular season ended and crews were able to tear down the old scoreboards. The North End Zone construction revolved around the addition of a massive elevator shaft for six new elevators, the new party deck that sits on top the stadium roof, and the new Mitsubishi Diamond Vision Video Board.
The work in the South End Zone is even more extensive: to support the structures for the new video board and the new seating, an outer ring was added to the existing bowl and three new levels were built on top of the existing three levels. This is where the majority of the added seating will be, as well as indoor shops and concessions. It also requires the most reinforcement of the existing steel columns.
This reinforcement included extending base plates and adding plating and bar stock to the columns. On some of the base plates this called for v-groove welds that required pounds of filler metal to be added to the joint. New plating and bar stock were added to help bear the weight and required multi-pass welds up to one-inch wide and six-feet long. Much of this work was done with E7018 stick electrodes in the past. While the Stick process is self-shielded and provides proven quality, it can be slow and, in a heavy deposition application such as this, can result in a substantial waste of filler metal from the leftover electrode stubs.
Benefits of Self-Shielded Flux-Cored Welding in Structural Steel Applications
A number of ironworkers on the project worked with their local union hall to achieve certification in the self-shielded flux-cored arc welding process, and a number of the ironworkers on site already had their certifications. Miron Construction worked with Miller and Hobart Brothers to determine the best equipment and filler metal combination for this application, and welding engineers from Miller visited the site to work with the ironworkers to answer questions and provide guidance as needed. The final solution featured XMT® Series multiprocess welding inverters matched with SuitCase® X-TREME 12VS voltage-sensing wire feeders from Miller, and Fabshield® XLR-8™ (E71T-8JD H8) self-shielded flux-cored wire from Hobart Brothers. Like Stick welding, this combination and process requires no shielding gas and is capable of being used in outdoor welding applications where wind is common. The ironworkers began noticing benefits immediately compared to traditional Stick welding.
Self-shielded flux-cored arc weldingoffers:
• Increased welding speeds (the ability to make more feet of weld per day)
• Increased deposition rates (the ability to lay down more pounds of weld metal per day)
• Increased filler metal efficiency (substantially less filler metal is wasted in the process)
The benefits of the process were specifically noted in a stretch of six-foot long bar stock reinforcements ranging from 2.5-x 2.5-inches to 5- x 5-inches in width. Adding these reinforcements required multiple passes to achieve a minimum 5/16-inch weld leg. Ironworkers switched from a 1/8-inch stick electrode to the 1/16-inch diameter self-shielded flux-cored wire. Typically, where you would run the 1/8-inch stick electrode at 140 amps to achieve a deposition rate of 2.89 pounds/hour, the 1/16-inch flux-cored wire allows the operator to run at 240 amps to achieve a deposition rate of 4.67 pounds/hour. This substantially increases productivity.
“We’ve got about 30 percent less time with the (flux-cored) wire,” says Ken Wirkuty, an ironworker on the project with Miron Construction Co., Inc. “You can keep burning it, you can get a little wider pass than you can with stick if you get it set right.”
A number of things can play into the increased productivity Wirkuty mentions. Self-shielded flux-cored arc welding allows for faster travel speeds and actually allows you to deposit more metal into the weld with each pass. There is also substantially less starting and stopping with self-shielded flux-cored arc welding as the wire is continuously fed compared to Stick welding where you are constantly replacing stick electrodes. That practice also leads to a substantial waste of stick electrodes: many welders will discard a rod before it is burnt completely down and switch to a new rod.
“When you’ve got the wire, you have very minimal loss of your products,” says Ken Wirkuty. “On stick, you get arc strikes, guys throwing them out, getting a new one. You might only burn half a rod, then you’re on to a different rod and you’ve got quite a bit left over in a 50-pound box when you’re all said and done with it.”
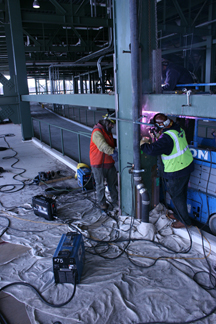
greater travel speeds, greater weld
deposition and a more efficient use of
the weld filler metals.
Self-shielded flux-cored wire typically offers higher deposition efficiency than stick electrodes. A standard stick electrode may deposit anywhere from 50-73 percent of its mass into the weld joint. The rest of the electrode is lost through its stub. In this case, a 50-pound box of electrodes may only deposit 30 pounds of weld metal. Flux-cored wires, however, deposit about 75-80 percent of its total mass. This allows users to purchase less filler metal per joint due to the higher deposition efficiency.
Welding Systems Ease Conversion
The equipment and filler metals presented for this application are each designed to not only improve productivity, but also to simplify the training process. Some training will have to take place (this specific wire requires using a drag motion instead of a push technique in the vertical up position, for instance), but most welders will pick up the technology with relative ease. Highlights of the systems put to work at Lambeau include:
XMT Series Multiprocess Inverters: Small and compact, these versatile welders are popular for their DC multiprocess capabilities (Stick, MIG, TIG, Flux Cored) and can easily be moved around the jobsite as needed. These inverters also offer input power flexibility and technologies that ensure consistent arc performance on jobsites like this where there is a large demand for power. Specific to this jobsite, the ability to perform both Stick and Self-Shielded Flux-Cored welding is critical as both applications are used regularly.
SuitCase X-TREME 12VS Wire Feeder: Built to be durable and face the rigors of life on a construction site, these extremely portable voltage-sensing wire feeders also offer excellent arc starts and improved arc performance for all types and sizes of wires. As the wire feeder runs off of open circuit voltage, it does not require an extra control cable—eliminating clutter and hassle. The feeder also offers a trigger hold function that improves operator comfort on long, continuous welds. The potted and trayed main circuit board helps protect the machine and ensure excellent reliability in the harshest of environments.
Fabshield XLR-8 Self-Shielded Flux-Cored Wire: This wire requires no shielding gas and is perfect for welding outdoors in construction applications. This particular wire provides a low hydrogen weld deposit and high impact strength properties at low temperatures to resist cracking, excellent out-of-position performance even at high current levels for increased productivity, excellent mechanical properties under a wide range of heat inputs, and excellent slag removal for increased productivity and reduced slag entrapment.
This is an optimal combination for this specific application. While Stick welding will always have its place in the construction industry, high-deposition applications like this where you’re depositing heavy amounts of weld metal are perfect for making the switch to Self-Shielded Flux-Cored welding.
“So far, the advantages of running the wire have been the speed and productivity of it,” says Jake Wirkuty, Ken’s brother and a fellow ironworker. “You’re cutting the weld time almost in half for some of these guys that are proficient in running the wire compared to Stick.”