Out-of-Position Welding with MIG and Flux-Cored Processes
Out-of-position welding undoubtedly presents challenges, but it is also unavoidable in some welding operations. Large components in industries such as shipbuilding, structural steel, pipeline and general fabrication may not be practical to move into easier-to-weld flat or horizontal positions. Or in some instances, a workpiece may be fixed in place.
In either of these scenarios, welding operators must weld out of position. The key is to understand the challenges of this technique and avoid common mistakes. It is also important to understand the advantages and limitations of different welding processes for the application — for example, choosing between (MIG) or gas-shielded flux-cored arc welding (FCAW-G).
Both are common welding processes that allow the welding operator to achieve high productivity when welding in position, but they vary in their capabilities for out-of-position welding.
Considerations for out-of-position welding
Gravity is the biggest challenge when welding out of position — vertical or overhead — since the weld pool drips downward. This makes it harder not only to produce quality welds, but also to maintain higher levels of productivity. Welding operators tend to reduce heat input, which influences the fluidity of the molten metal and slow their travel speeds to control the weld pool.
An important factor for gaining success in these applications is welding operator skill. The welder must be trained in proper techniques for welding out of position with the MIG or FCAW-G process, as they differ from in-position welding.
It is also critical to use the most appropriate filler metal and set the welding parameters accordingly. Solid wires like American Welding Society (AWS) ER70S-6 are the most common for out-of-position MIG. AWS E71T-1 gas-shielded flux-cored wires for FCAW-G are classified to be used out-of-position and can be used with higher heat inputs, providing increased deposition rates.
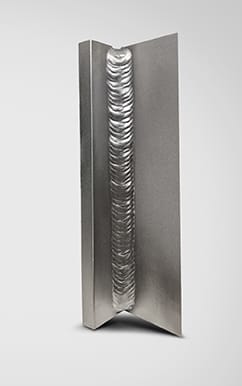
The MIG process
MIG with solid wires or metal-cored wires can be, and often is, used to make acceptable welds out of position. This is especially true when welding thinner materials and on smaller applications, although it can be used for thicker materials at times. However, if there is a lot of welding required on larger parts, this process may not be the best option.
To help control the weld pool, out-of-position MIG requires the low heat input of short-circuit transfer or pulsed welding. When welding with the short-circuit transfer, some amount of spatter should be expected. The pulsed MIG process can help combat issues with spatter and also provide a slight improvement in deposition rates for the same heat input compared to short-circuit.
The pulse process, however, isn’t a simple or guaranteed solution for the challenges of welding out of position with MIG and equipment with this capability tends to be more expensive. The process still requires close attention to welding parameters and welder technique to be successful.
As previously mentioned, in vertical-up MIG, welding operators need to lower the welding parameters to decrease heat input. However, using colder parameters can cause some negative repercussions — namely, the potential for lack of fusion and lower deposition rates. It also requires a higher level of skill to produce acceptable welds due to the tendency of welds to have excess reinforcement or convexity.
Welding vertically down with MIG can help recoup some productivity but obtaining adequate fusion can still be difficult. Also, vertical down welding is not allowed in certain applications and industries due to code requirements. Always be sure to follow welding specifications for applications that must be completed to code.
For out-of-position MIG, the welding operator will often be required to employ a weave technique to obtain the acceptable bead shape and fully wet into the toes of the weld.
The FCAW-G process
Compared to MIG, out-of-position FCAW-G is more productive. It is also more tolerant to variations in parameters, as well as welding operator skill and technique. In fact, gas-shielded flux-cored wires, such as E71T-1, are capable of more than doubling out-of-position deposition rates. This is due to a fast-freezing slag that keeps the molten weld pool from falling out of the joint, plus the slag system allows the wire to provide excellent wetting and a flat weld profile.
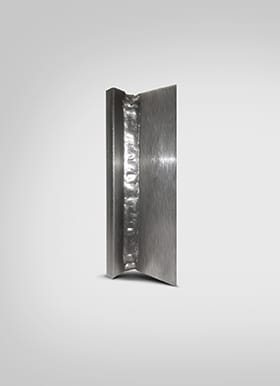
Typically, FCAW-G is used out of position in heavy, industrial applications, often where positioning large parts is less feasible and mill scale and oxides on the base material are more prevalent. The presence of mill scale can make proper fusion and ideal weld profile (shape) a challenge; however, the greater joint penetration of flux-cored wires from using higher heat inputs helps mitigate the issue. The slag system and additional deoxidizing elements in these wires are also beneficial to overcome the challenges of welding on steels with oxide and scale on the surface.
In terms of welding operator skill and technique, out-of-position FCAW-G requires much less need for manipulation or weaving to achieve the ideal weld contour. There is also higher tolerance to variances in welding operator technique and consistency; therefore, the process requires less skill to produce welds that can pass inspection.
There are limitations to FCAW-G compared to MIG, particularly the need to clean slag in either single- or multi-pass applications. This may require an additional step that can have an impact on productivity. Also, extra ventilation or personal protective equipment (PPE) may be more critical to protect the welding operator.
Other considerations
When deciding between MIG or FCAW-G, it’s important to think about the volume of work at hand. If a welding operation has a large volume of out-of-position applications, FCAW-G can definitely bring higher levels of productivity and at a reasonable cost even though flux-cored wires are often more expensive than solid wire. Conversely, if a facility only has a small percentage of out-of-position requirements, it may make sense to use a cleaner solid wire or metal-cored MIG wire that doesn’t require additional post-weld cleaning to remove slag. Remember, labor for additional cleaning adds to an operation’s overall expense.
In some cases, a welding operation may opt for both processes as a matter of streamlining their applications. This approach is made possible by using dual wire feeders with flux-cored wire on one side and MIG wire on the other, paired with a power source capable of constant voltage (CV) and pulsed MIG welding.
If questions about the best process or techniques for out-of-position MIG and FCAW-G arise, contact a trusted welding distributor, filler metal manufacturer or equipment manufacturer.
Republished from Welding Journal (March 2021) with permission of the American Welding Society (AWS). Click here to view the original article.