Aluminum Metallurgy Basics for Welders
Aluminum alloys are split into series that are based on the primary alloying elements added, ranging from 1xxx – 8xxx series. These series can also be grouped into two classes that are based largely on the strengthening methods used: heat-treatable and non-heat-treatable alloys.
In the former, alloys can gain significant strength through heat treatment at specific temperatures and times; the latter alloys get their strength mainly through solid solution strengthening and coldwork. Each alloy series has its specific advantages and usages.
Non-heat-treatable aluminum includes four distinct alloy series that are usable for specific applications. Each has a main element that provides its strength and other characteristics.
1xxx is pure aluminum that provides excellent electrical conductivity and corrosion resistance for welding chemical tanks.
3xxx includes higher levels of manganese (Mn) and provides good thermal conductivity for welding heat exchangers.
4xxx is known for its weldability for general applications and includes higher levels of silicon (Si). There are also some heat-treatable 4xxx series alloys.
5xxx contains magnesium (Mg) as a main element and works well for general structures and truck fabrication due to its welded strength.
The heat-treatable aluminum alloys also include four alloy series that feature specific characteristics for their intended applications:
2xxx includes higher amounts of copper (Cu) that increase tensile strength, making it a good choice for use in the aerospace industry.
4xxx that is heat-treatable is known for its castability and contains Si as its main element.
6xxx works well for color matching in structural and architectural jobs and includes higher levels of both Mg and Si for strengthening.
7xxx contains Zinc (Zn) for strength and is often used for fabricating sports products.
The 8xxx series are novel alloys with unique alloying additions and are not commonly used.
This article will break down the strengthening methods in these alloys and how the extreme heat from arc welding affects them.
Metallurgy and metal microstructure
In order to understand the physical phenomena involved in the strengthening and welding of aluminum alloys, it’s important to start with a brief overview of metallurgy and metal microstructure. The vast majority of metals exhibit polycrystalline microstructures, meaning that the metal atoms arrange themselves in a repeating pattern called a crystal lattice to form crystals (also called grains). There are many of these crystals at different orientations to each other that form the bulk of the material (note that single crystal and amorphous metals do exist through special processing techniques). In addition, each metal has its own characteristic crystal structure, ranging from very simple to quite complex. While many of the concepts presented apply to most metals, from here on the focus will be on aluminum.
Within the aluminum crystal structure, there are inevitably defects or variances. There are multiple types of defects possible, but of particular interest are defects called dislocations.
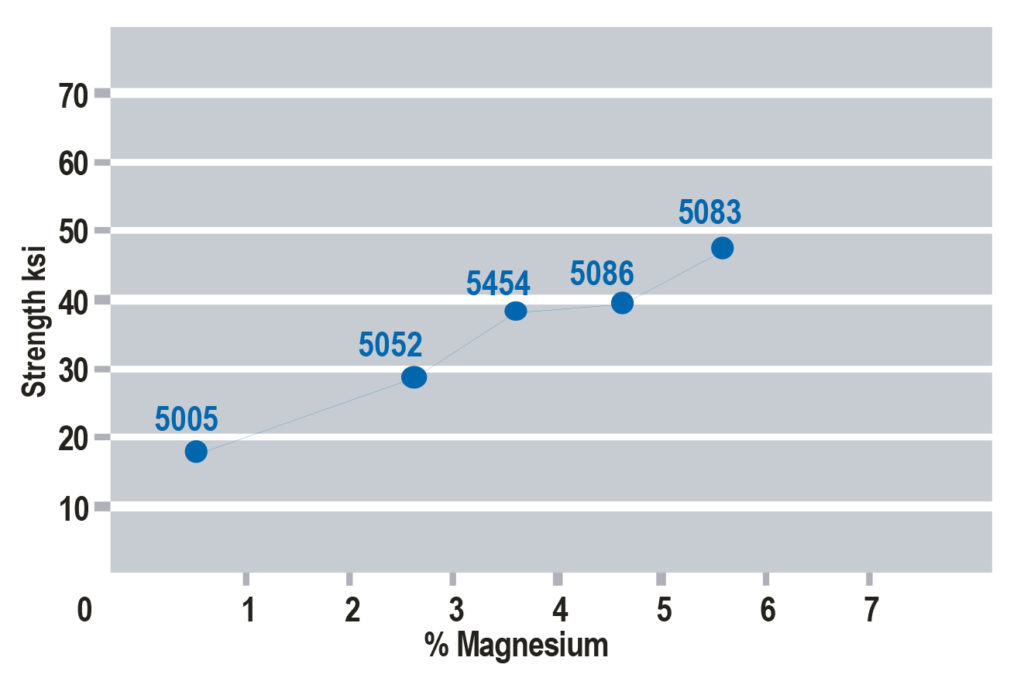
increases in selected 5xxx series aluminum alloys.
Several types of dislocations can occur, but in general dislocations are either mobile or immobile and the mobile dislocations are the focus here. These dislocations can move throughout the aluminum crystals, which is largely what makes plastic deformation possible in aluminum versus, say, brittle ceramics. Without dislocation motion, plastic deformation is not possible. This idea of dislocation movement is crucial for understanding strengthening methods; the basis of strengthening aluminum is inhibiting dislocation motion, so to make aluminum stronger barriers must be created to dislocation motion. There are very in-depth analyses of dislocations and their movements, breaking and forming of metallic bonds, interactions with barriers and thermal activation, but these basics should be helpful in gaining a better understanding of aluminum alloys and welding.
Strengthening methods
There are multiple strengthening methods found in the two groups of aluminum alloys, and they all relate back to the concept of dislocation motion. Non-heat-treatable alloys do not see appreciable strengthening from thermal treatment, and instead get strength from other elements in solution with the aluminum and through deformation processes. Consider 5xxx series of aluminum, in which magnesium (Mg) is the primary alloying element.
Certain elements, such as Mg, have considerable solubility in aluminum. These elements fit within the crystal structure of aluminum; either substitutionally, replacing aluminum alloys within the crystal structure, or interstitially, fitting between the aluminum atoms. In either case, there is a size mismatch between the aluminum atoms and the alloying elements that presents a strain on the crystal lattice, and this held strain inhibits dislocation motion and adds strength to the metal. As more Mg is added to aluminum, strength is increased (note there are limits to this).
This is the process known as solid solution strengthening; alloying elements in solution adds strength to the metal by inhibiting dislocation motion. It is worth noting that certain elements have more solid solution strengthening potential than others. Mg is one of the most potent solid solution elements, which is why the 5xxx series is so widely used. A chart showing the strength increase from Mg additions is shown in Figure 1.
In wrought aluminum alloys, the metal can be coldworked (deformed at low temperature) to add strength and is once again related to dislocation motion. Deforming the aluminum does two things to add strength: residual stress is stored in the metal, and the metal grains or crystals are deformed, which results in increased dislocation density and grain boundary area. Both work against dislocation motion, adding strength to the aluminum. An illustration of the grain structure changes is shown in Figure 2.
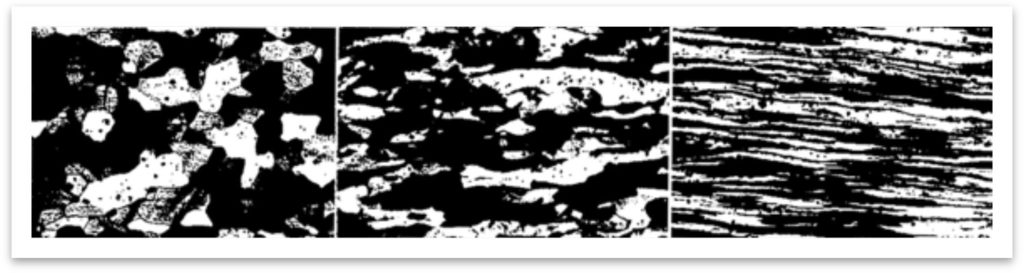
with permission of ASM International. All rights reserved. www.asminternational.org
The strengthening mechanism in heat-treatable alloys is different but still relates back to dislocation motion. In aluminum alloys, the bulk of the material carries the same crystal structure, all existing as a single phase called the primary phase. In heat-treatable aluminum, alloying elements are added that can then form secondary phases, often called precipitates. This happens when sufficient heat and time allow the alloying elements to diffuse through the material and form separate structures in a process referred to as heat treating or aging.
These secondary phases generally exhibit a crystal structure that is different from the primary phase, with varying degrees of dissimilarity. Secondary phases can be found in many alloys, including non-heat-treatable aluminum alloys, but not all secondary phases add strength to the metal. The heat-treatable aluminum alloys, such as the 6xxx series, form secondary phases that do add strength. The exact interaction between dislocation motion and precipitates can be complex, but in essence these precipitates add strength by resisting dislocation motion.
The effect of welding on aluminum
In aluminum arc welding, the arc reaches many thousands of degrees in temperature. As a result, there is a large amount of heat that is transferred to the base material surrounding the weld. This area is known as the heat-affected zone (HAZ) and sees significant effects from the heat. The exact physical effects of this heat are different for heat-treatable and non-heat-treatable aluminum alloys, but in both, heat input from the process alters the base material and creates loss of strength. A smart weld design accounts for those strength losses to ensure the integrity of the completed weld.

zone, partially annealed zone and unaffected zone. Reprinted with permission
of ASM International. All rights reserved. www.asminternational.org
In non-heat treatable aluminum, strength gained from solid solution as explained before is inherent to the chemistry and is generally not affected by the heat from arc welding. However, the fine, deformed grains and stored strain seen in coldworked aluminum are greatly affected. The heat provides energy for new grains to form and grow, resulting in a much coarser and softer microstructure, and also releases the stored energy from coldworking. This thermal process is known as annealing, and the formation of new grains is recrystallization. The effect of heat lessens further away from the weld, and there are certain zones in the base material.
The farthest from the weld is the unaffected zone, in which the grains remain the same as at the end of the coldworking. Moving closer to the weld is a partially annealed zone, where some new grains form and some of the stored stress is relieved, and then the annealed zone where large grains form with random orientation and all the stored stress is released. Finally, there is the fusion zone — the point at which the filler metal and base metal have completely melted, solidified and cooled. An illustration of these zones is shown in Figure 3.
The effect of the welding process and heat input on heat-treatable aluminum differ from non-heat-treatable aluminum. One constant, however, is the strength losses that occur along the way.
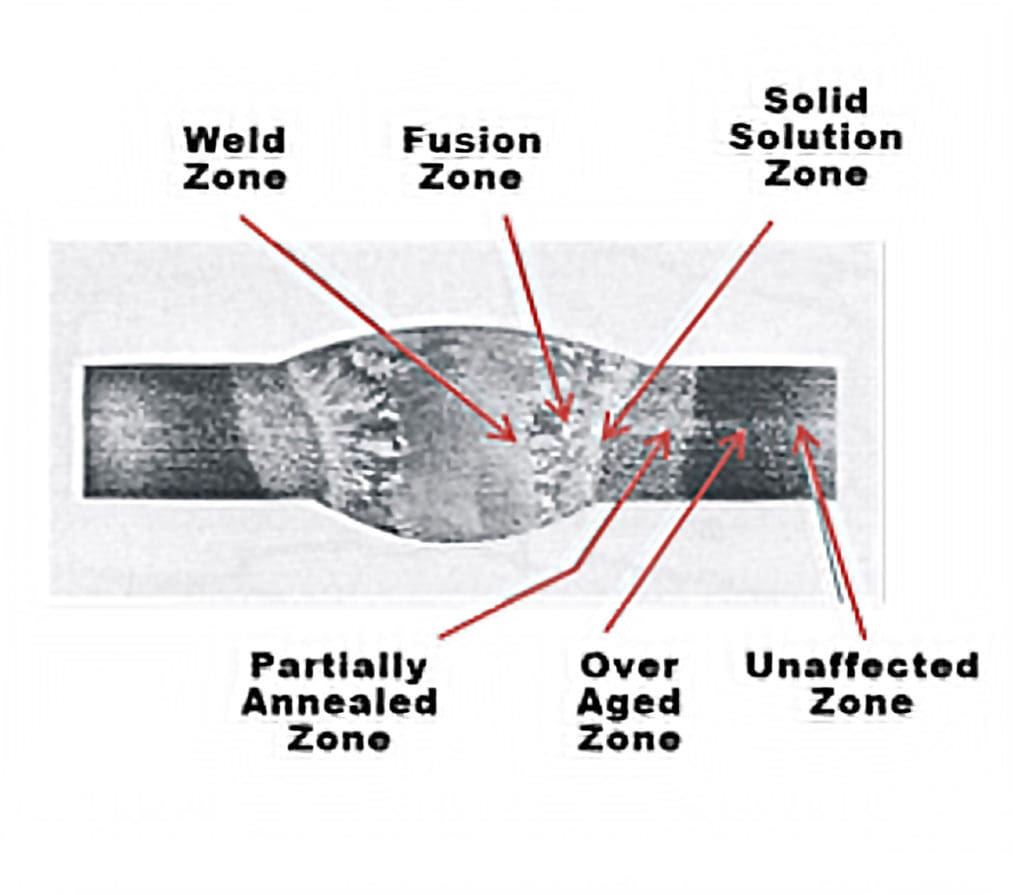
zones in welding heat-treatable base metal. Reprinted
with permission of ASM International. All rights reserved.
www.asminternational.org
Heat input alters the grain and precipitate structure when welding heat-treatable aluminum. At the weld zone — the center point of the weld that has been liquified from the welding arc and re-solidified —the weld itself is primarily made of filler metal.
Moving outward from the center weld zone, the fusion zone is a combination of filler metal and the aluminum base metal that has been liquified and solidified. It can be stronger than the weld zone. Beyond that is the solid solution zone, where the aluminum hasn’t liquified but the temperature from the welding arc was high enough that precipitates have return to solution.
The over aged zone in the aluminum weld is exposed to the high enough heat inputs from the arc to over-age all of the precipitates in that part of the weld, making them coarse and resulting in loss of strength. Finally, there is the unaffected zone in which the aluminum is in its original state. An illustration of these zones is shown in Figure 4.
Conclusion
Aluminum is considered by many to be difficult to weld, but it doesn’t have to be. Gaining insight into the basic metallurgy of the material can help welders achieve a better understanding of how the material reacts to heat during the welding process and how to better work with it. Starting with proper technique, it is possible to establish practices that can make welding aluminum and design easier.
Republished from Welding Journal (February 2021) with permission of the American Welding Society (AWS). Click here to view the original article.