NASA Chooses New Aluminum Filler Metal 4943 For Their James Webb Space Telescope Project
Alloy 4943 is the first aluminum filler metal that was developed in the USA, designed for use in wrought commercial applications, and to be registered with the Aluminum Association in over 50 years. This new aluminum filler metal has recently received AWS A5.10 classification, ASME filler metal material group allocation of F23, and Canadian Welding Bureau and American Bureau of Shipping approvals. The new 4943 filler metal was designed primarily to provide a consistently high strength alternative to filler metal 4043, in the as-welded condition, while maintaining the ease of welding and other advantages of 4043.
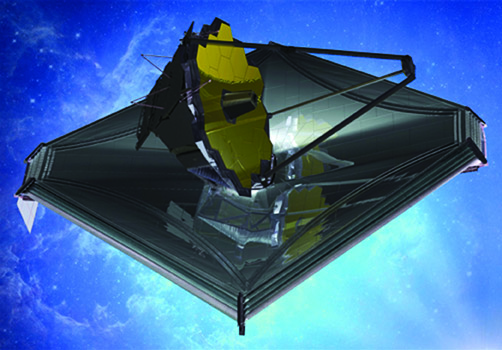
impression.(Photo courtesy of NASA)
During the first 2 years of the development and testing of this new filler metal a number of aluminum fabricators favorably evaluated its performance. But possibly the most interesting and comprehensive series of third-party tests were conducted by NASA at the Goddard Space Flight Center for the James Webb Space Telescope project.
About The New James Webb Space Telescope (JWST)
The James Webb Space Telescope (JWST) is the scientific successor to Hubble Telescope and its goals were motivated by results from Hubble. The JWST will “go beyond” what Hubble has already done by looking at light with longer wavelengths (infrared). This ability allows it to see light from more distant objects whose visible light is degraded over the vast distance of space from UV and optical into near-infrared. To optically “see” these vast distances a larger mirror is also required. The JWST primary mirror is 6.5 meters wide, which is about 7 times the collecting area of Hubble’s 2.4 meter wide primary mirror (see figure 1). To support such a large mirror, JWST itself is a massive engineering feat. This project includes a sun shield almost as big as a Boeing 737 to protect the heat-sensitive telescope from our own sun’s radiation.
The science that JWST will explore goes further and deeper into our knowledge of the universe than ever before by having the capability to study the assembly galaxies, observe the birth of stars and protoplanetary systems, analyze the chemical properties of planetary systems including our own, and see the first bright objects that formed in the early Universe. All of these amazing capabilities are achieved by the telescope’s cutting edge cameras which are called science instruments (SI). All four of the SI’s are supported by a precision-optical frame called the ISIM (Integrated Science Instrument Module). One of the multiple testing operations is known as a CryoVac test in which the functionality of the ISIM is evaluated in Goddard’s Space Environment Simulator (SES) where the cryogenic temperatures of 427 Deg. F and vacuum of space are recreated.
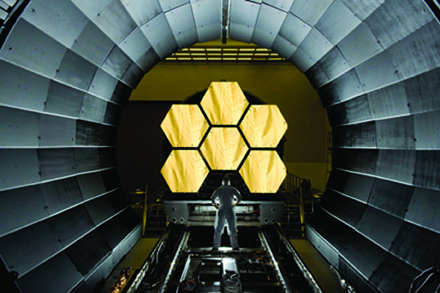
Webb SpaceTelescope’s primary mirror segments are prepped to begin
final cryogenic testing at NASA’s Marshall Space Flight Center.
This represents the first six of 18 segments that will form NASA’s
James Webb Space Telescope’s primary mirror for space observations.
Engineers began final round-the-clock cryogenic testing to confirm that
the mirrors will respond as expected to the extreme temperatures of
space prior to integration into the telescope’s permanent housing
structure. (Photo courtesy of NASA)
Developing Welding Procedures to Meet Strength Requirements
While safely supporting the ISIM during integration, performing CryoVac, and other testing was an extreme engineering challenge in itself, imposed test requirements, strength margins, and design envelopes demanded a strong, light-weight aluminum 6061 frame which was termed the SES Integration Frame (SIF) (see figure 2). Early design iterations revealed that a welded frame was needed to achieve the weight requirement but standard welding strength values did not achieve the design margins needed. It was learned that the post-weld aging process used in specialized industries could achieve the strength needed. The SIF matured as a multi-rolled integration and testing frame that would support and lift the ISIM as well as hold needed test equipment in close proximity around the ISIM.
An in-depth development study was completed to determine which filler metal, 4043, 4643, or 4943 would meet their design needs. After conducting tests to compare the new 4943 filler metal with 4043 and 4643, the test results identified significant improvements in strength from the 4943 filler metal over the other filler metals tested and also established that the 4943 weld wire would maximize the frame’s performance.
The following is a quote from Matthew Stephens, Mechanical Engineer, Goddard Space Flight Center “After working on improving hand welding and cooling techniques with the fabrication vendor, we finished another round of transverse weld tests with stunning results. The average sample strength was 40 ksi with a range between 36 & 44 ksi, which were based on 12 samples between two different welders. The cooling techniques used pushed several of the failures from the HAZ to the fusion zone in which case the 4943 was the factor enabling the unprecedented high ultimate strength values. In-field hardness measurements proved that the frame itself achieved these same post-weld aged strength levels proving that these results were not just possible in a laboratory but a manufacturing environment as well. The 4943 weld wire seamlessly merged with our welder’s existing techniques and has proved to be a key technology, along with good welding practice, in reaching the high strengths we needed”.
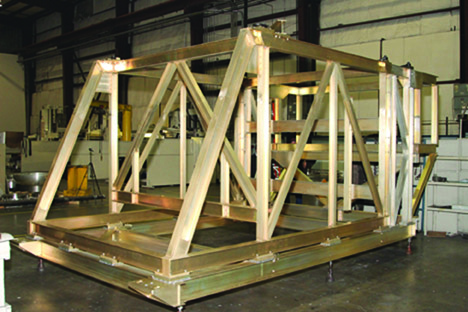
performing CryoVac, and other testing was an extreme engineering
challenge in itself, imposed test requirements, strength margins, and
design envelopes demanded a strong, light-weight aluminum 6061
frame which was termed the SES Integration Frame (SIF).
(Photo courtesy of NASA)
How does the 4943 filler metal provide higher strength?
Unlike steel welding, for reasons associated with weld integrity and strength, filler metals with significantly different chemical composition than that of the base metal are often used when arc welding aluminum. When arc welding with the 4043 filler metal, particularly on the 6xxx series base metals, it is important to recognize that the completed weld bead chemical composition, resultant weld integrity, and mechanical properties are dependent on the mixture of the base metal and the filler metal in the weld bead.
The strength of a weld made with filler metal 4043 (which has no other strengthening additives other than silicon) is often dependent on dilution with the base metal. Weld beads (that are a mixture of filler metal and base metal) can acquire small amounts of magnesium from the 6xxx series base metals. The addition of magnesium to the 4043 filler metal, obtained from dilution of the base metal, combines with the silicon in the 4043 and produces magnesium-silicide (Mg2Si), a very effective strengthening precipitate. One problem associated with this method of weld bead strengthening is its unpredictability. When arc welding the 6xxx series aluminum base metals with the 4043 silicon based filler metal, there are many situations when the dilution ratio between base metal and filler metal can fluctuate, and influence the strength of the completed weld.
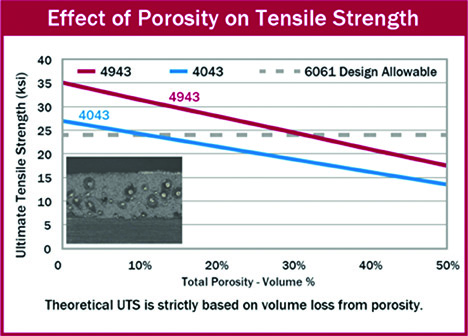
room for discontinuities in a weld (porosity for example) before the
weld drops to below the acceptance strength level.
4943 – The Higher Strength Alternative to 4043
Aluminum filler metal 4943 was developed with the objective of providing a consistently higher tensile, yield, and shear strength alternative to 4043 while maintaining the same proven welding characteristics of 4043. The 4043 filler metal is a popular aluminum/silicon filler alloy for general purpose welding applications. However, it has lower strength when compared to the 5xxx series filler metals, and can show significant variability in strength based on welding conditions. The 4943 filler metal has been formulated to be welded with similar weld procedure specifications as 4043, provide improved strength, and address variability in strength issues. While improving weld strength, 4943 will also maintain the same excellent corrosion characteristics, low melting temperature, low shrinkage rate, higher fluidity, and low hot-cracking sensitivity as the 4043 filler metal, and also exhibit low welding smut and low discoloration. In addition to consistently higher as-welded strength, the new 4943 filler metal is also heat treatable and has demonstrated its improved strength characteristics in the post-weld solution heat-treated and artificially-aged condition when compared to the currently used heat-treatable filler alloy 4643 (which has been generally employed for welding the 6xxx series base materials that are post-weld heat-treated).
The Strength Benefits of 4943
In full penetration groove weld applications the as-welded strength of 4043 without dilution is typically adequate to support the 24ksi minimum transverse tensile strength requirement of 6061-T6, which is set as a result of the depleted strength of the base material Heat Affected Zone (HAZ). However, the lower strength weld produced by 4043 leaves less room for discontinuities in a weld (porosity for example) before the weld drops to below the acceptance strength level – see Figure 3. Although 4943 will provide improved strength in groove welds, this is not its principal intended benefit. The principal benefit of 4943 is to provide higher strength fillet welds.
The most important benefit of 4943 is to provide consistently higher strength fillet welds. There are far more fillet welds than groove welds used in structural welded components, of all aluminum welds in industry, approximately 80% of them are fillet welds. Fillet welds, by design, are partial penetration joints which are assumed to have minimal base metal dilution. Unlike full penetration groove weld transverse tensile strength, which is controlled by the base metal Heat Affected Zone (HAZ), fillet weld shear strength is directly controlled by the strength of the filler metal used during welding.
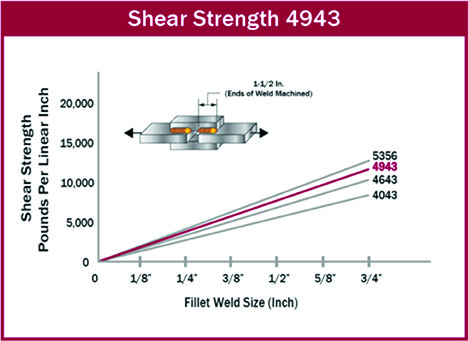
higher strength fillet welds.
Tests comparing 4043 to 4943 have shown 4943 to have an ultimate tensile strength that is conservatively 20% higher than 4043. One potential benefit of this substantial increase in weld strength may be the opportunity for a manufacturer to decrease the size of fillet welds while maintaining the same strength. This may provide potential savings to a manufacturer from the reduced amount of weld wire needed to be purchased for a project, and also, in the labor cost which could be reduced from the time saved by making smaller welds (increased productivity). One other side benefit to smaller welds, which is often very important, is reduced distortion. With the increased strength of 4943 over 4043, it is quite plausible to consider a one pass fillet weld made with 4943 having the same strength as a three pass weld made with 4043. Figure 4 shows the relative shear strength of 4043, 4643, 4943, and 5356.
Conclusion
Aluminum-silicon alloys of the 4xxx series are widely used in GMAW (MIG) and GTAW (TIG) welding because of their excellent welding characteristics, fluidity, reduced shrinkage distortion, and resistance to hot cracking. The moderate and variable strength of 4043 can be improved via magnesium additions to the filler alloy itself, and this was achieved to some extent with alloy 4643. The magnesium addition was optimized with a silicon addition in alloy 4943 for improved characteristics relating to strength, fluidity, shrinkage and hot cracking resistance. Test have shown that when using filler metal 4043 for full penetration groove welds we can come very close to the minimum design strength allowable for 6061 base metal and that this concern becomes far less significant if we use the higher strength 4943 filler metal. However, the principal advantage of the 4943 filler metal over 4043 would appear to be when used for fillet welds. In the fillet weld application there is a distinct opportunity for improving weld strength, reducing welding costs, and improving productivity, by using 4943 filler metal over 4043. Welds made using the new filler metal 4943 can exhibit substantial improvements in strength when compared with 4043 and/or 4643 filler metal in both the as-welded and post-weld heat-treated conditions.