Metal-Cored Wire Helps Arizona Company Improve Productivity
Standardization and repeatability have become popular buzz-words in the welding industry as it continues to adapt itself to lean business models. These practices have focused in part on establishing protocols that create uniformity of quality and appearance for every product that leaves the shop, regardless of who welded it or when it was welded.
Sometimes, however, there is no amount of standardization that can overcome the “human element.”
When the city of Phoenix decided to build its light-rail system terminals, it selected a design consisting of exposed steel columns for the canopies under which its riders would wait for the next train. The columns were constructed of two 4- X 6-in. rectangular tubes, each “sandwiched” between two pieces of plate steel and connected by another length of plate steel.
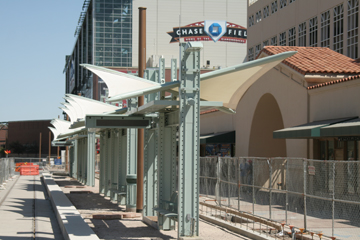
canopies provides shade to riders outside of Chase Field,
home of the Arizona Diamondbacks.
Being exposed, the columns called for very high quality and visually pleasing welds. The welding sub-contractor initially hired for the project produced welds with frequent starts and stops along the length of the columns as well as inadequate penetration, both of which failed to meet the city’s quality and uniformity requirements.
Given the chance to take over the job, Arizona-based Skyline Steel knew from the beginning that the only way they could meet the job’s demands would be through automation—a technology they had never ventured into before.
With the help of, Jim Kelley and Joel Ashmore with Praxair, FabCOR® 86R wire (formerly Tri-Mark® Metalloy® 76) from Hobart Brothers, the Dimension™ 1000 from Miller Electric, and Bernard’s Centerfire™ consumables, the company not only met the city of Phoenix’s stringent demands, they were also able to double their anticipated profit and position themselves to expand their business into new markets.
From Humble Beginnings
Since its beginnings as a carport fabricator in 1983, and through its growth into structural markets and beyond, Skyline has prided itself on providing a consistent and high quality product at a reasonable price.
“When a buyer goes to a seller, they expect a consistent product and consistent service at a consistent, good price,” explained Skyline President Rick Dancer. “Meeting those expectations has been an integral part of our success. In order for us to provide that level of quality to our customers, we likewise require it from our vendors.”
Those values enabled Dancer to take the company from a $250,000/year enterprise when he bought it in 1988 to a $35 million/year company today.
Another major contributor to the company’s success has been its willingness to take on new challenges and face new risks.
A New Challenge
The increased popularity in recent years of exposed architectural steel gives rise to some previously non-existent welding challenges. When the city of Phoenix’s Valley Metro transit authority decided to build its light-rail lines with steel and fabric canopies at their terminals, they wanted every detail of the canopies to be aesthetically pleasing, right down to the welds.
What they received from their original welding sub-contractor were submerged arc welds that did not adequately penetrate the joints and semi-automatic welds that contained numerous inconsistencies where the welders repositioned themselves to continue along the length of the steel beams.
The project called for a 3/8- X 4- X 6-in. rectangular tube sandwiched between two 1/2- X 8-inch wide plates. Two “sandwiches” would then be linked by a 6-in. plate. Once assembled, four canopy arms needed to be added before the entire assembly was painted and installed in the Phoenix light-rail terminals.
The tricky part was that they could not grind the welds, and the welds needed to be completely uniform, without any starts and stops, for lengths up to 30 feet. All together, the project required 850 canopies with a total of over 8.5 miles of perfectly symmetrical, continuous welds. Plus, the team had less than three months to go from testing and sample evaluation to full-scale production.
When Phoenix’s city planners decided that the welds on the first set of canopies were not good enough, the project’s general contractor, Archer Western, turned to Skyline Steel.
“Archer Western called us because they needed a shop that was certified by the city of Phoenix,” recalls Dancer. “Their dilemma was that they needed thousands of linear feet of continuous flat welds. We knew right away that we would need to automate the process to avoid any discontinuities in the welds.”
Distributor support
Skyline also knew that if they were going to venture into automation, they would need assistance. After initial research into automated welding systems, Skyline turned to its Praxair representatives, Jim Kelly and Joel Ashmore. Kelly and Ashmore did some research of their own, and together the two companies came up with an automated welding system that they believed would meet the challenge.
Together, the team was able to produce an acceptable weld in one week where their competitor was unable to produce an acceptable weld in nine months of trying.
“Once we understood what the end result needed to be, we got together with our suppliers, Hobart Brothers, Bernard and Miller Electric, and we acquired the equipment and consumables to do some development work in our Phoenix laboratory,” explained Praxair Productivity Specialist Jim Kelly. “Along with that, we decided to use a proprietary gas mixture to increase their deposition rates and an automated linear travel system to achieve the continuous welds.”
That dedicated support has earned Praxair reciprocal dedication from Skyline.
“We’ve had outstanding support from Praxair,” Dancer said. “If they weren’t as supportive as they have been, we wouldn’t have been successful with this project. Going forward, they have earned my confidence and will always get the first look at any of our future ventures.”
“It was a bit of a gamble,” Dancer said. “We took a chance with this, but it’s turning out to be everything and more than what we even expected.”
The Wire
Skyline and Praxair chose the 1/16-in. FabCOR 86R metal-cored wire from Hobart Brothers because it produces a high deposition, aesthetically-appealing and spatter-free weld.
“The FabCOR 86R, combined with a proprietary Praxair gas blend, cut through minor mill scale, mill oil and other light surface contaminants and still produced a spatter-free, slag-free weld,” Praxair’s Jim Kelly said.
Using 400-lb. drums instead of individual spools of wire greatly reduced the overall cost and footprint of the wire, and it reduced production downtime associated with spool changeovers.
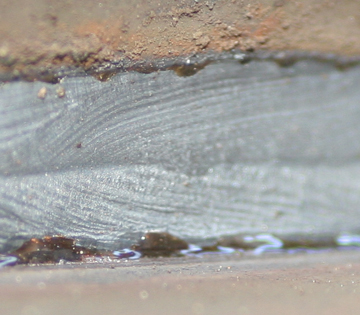
high-quality, continuous welds with very little spatter and a
visually appealing bead profile.
“When we calculate production cost, we don’t just take the cost of the product into the full cost equation,” explained Kelly. “So, although the FabCOR 86R wire costs a little more than some other types of wire, its increased deposition rates and larger payout drums reduce the labor costs, making the total per-pound-delivered cost much less expensive than other wires.”
Metal-cored wire is comprised of a very thin walled hollow metal sheath that is filled with metal powder and deoxidizers. The current flows primarily through the outer sheath of the wire, resulting in a more concentrated and conical welding arc than solid wire, which in turn produces deeper penetration and higher deposition rates than solid wire.
Metal-cored wire is usually used at relatively high amperages with a spray transfer process, which requires a shielding gas with a high argon content, typically 80 to 95 percent with the remainder carbon dioxide. The spray transfer process also produces smaller droplets of filler metal, which creates a calmer weld puddle. This wire also produces welds with very little spatter and a smooth, slag-free weld face, which reduces chipping, grinding, rework and other nonessential activities.
The Power Source
Sometimes referred to as the tank of power sources because of its durability, the Dimension 1000 provided the welding power for the project. Skyline and Praxair chose Miller’s Dimension 1000 power source for its reliability (especially at high temperatures) and its high duty cycle rating.
“We’re running a high amperage project with a large diameter wire, so we needed a machine that would have the power available to run continuously at those current levels,” explained Kelly.
Rated to 1000 amps at 100 percent duty cycle, the Dimension 1000 easily handled the current required for the project. In the beginning, Skyline tested a unit rated to 450 amps, which was able to handle the current, but just barely.
“We were bumping up against its duty cycle rating,” Shop Foreman Dan Henry recalls. “It probably would have been up to the task, but we didn’t want to take any chances.”
Instead, looking toward the long-term versatility and production capacity of their equipment, Skyline chose the Dimension 1000, knowing it would be able to handle not only the canopy project, but also future projects.
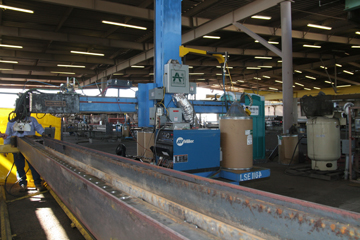
wire drum, welding arm and gun on a platform that travels
along a track, creating continuous welds on beams up to 30
feet long.
Another reason Skyline and Praxair chose a Miller product is that the company rates all of its welders to 104 degrees F, which helps to ensure the stated current levels will be available, even in the stifling Arizona heat. Since there is no specific standard that states what temperature to rate a welding power supply to, most manufacturers only rate their equipment to 86 degrees F. When it’s above 86 degrees F, the duty cycles start to drop drastically, affecting the capability of the power supply to keep up.
The Dimension 1000 offers direct current constant voltage (CV) capabilities for Gas Metal Arc Welding and Flux-Cored Arc Welding as well as constant current (CC) capabilities for Shielded Metal Arc Welding and Carbon Arc Gouging. It also features Fan-on-Demand™, which reduces the amount of airborne contaminants that enter the machine, and sealed circuit boards, which protect its electronic circuitry from contamination. By only operating when the welding arc is on, Fan-on-Demand™ also reduces power consumption.
Skyline and Praxair also chose the Dimension based on Miller’s reputation for quality and attentive customer service.
“One of the things I’ve found with Miller is that if I need to develop a project, I can call them up and they’re right there,” Kelly said.
The Gas
To further increase the deposition rates and provide a stable arc, Praxair recommended using a proprietary gas blend specifically developed for use in automated welding systems.
Using a standard C25 — 75/25 Argon/CO2 — would have been less expensive up front than the Praxair blend, but looking at the full cost of the welding operation, Skyline saw that the improved deposition rates of the Praxair mixture would more than offset the cost of the gas.
The Automation
Bringing together the wire, power source, consumables and gas was the automated linear welding system, consisting of a manipulator arm that travels at a distance that allows Skyline Steel to produce a continuous weld the entire length of the joint.
Torch-mounted feelers sense the joint and adjust the torch as needed while an operator observes through a custom made welding shade. A programming pendant allows the operator to remotely change the welding parameters if necessary.
The arm also holds the power supply and the wire, making the welding connections as sound as possible to eliminate potential welding flaws caused by poor connections in the welding cables when traveling such distances.
Almost immediately, the system was able to produce the continuous, flawless welds as required by the project.
To compare the difference between the automated system and the human element, they had one of their welders perform the same weld that the automated system was performing.
“It wasn’t pretty,” recalls Henry. “It took a long time and we still had the problem with starts and stops. This machine does the work of 10 guys, and the welds are perfect.”
Moreover, the automated system far exceeded everyone’s expectations by averaging a travel speed of 18-inches per minute and depositing 18 pounds per hour of finished weld.
“We’re producing at about twice the rate that we thought we would, and that we had to in order to make this a profitable endeavor,” Dancer said. “And since we’re producing at twice the rate we expected, we’re also profiting at twice the amount we expected.”
Part of that productivity is attributable to their perfect record in ultrasonic tests and reduced clean-up. “We test every column we manufacture and not a single one has failed ultrasonic testing,” Henry said. “Plus, there’s considerably less time spent in non-value added post-weld operations, such as chipping slag or grinding spatter.”
Just as importantly, they have exceeded their client’s expectations. “This job was way behind,” explained Henry, drawing a football analogy. “Archer Western came to us in the fourth quarter with two minutes left on the clock. We came through in the clutch and they’re happy with the results.”
Douglas Gabriel of Archer Western concurred. “Going with Skyline has helped us tremendously,” Gabriel said. “The process they implemented to get the canopies installed on time and to the required specifications was a major factor in our ability to complete the project on time.”
Moving forward
On its own, the success of the project made the equipment investment worthwhile, but the real payoff will come as Skyline uses the automated technologies and integrates the metal-cored wire into its other fabrication operations to win new business.
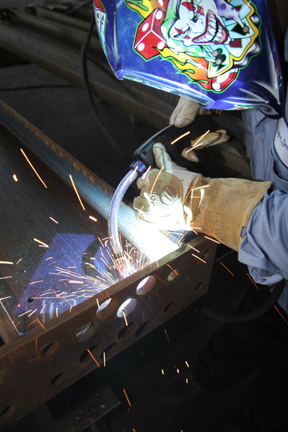
Centerfire consumables to their exact needs. The
products provide the company with more consistent
welds and have helped reduce downtime and costs.
“We’re now in a position to seek out new jobs that can take advantage of the capabilities of this system,” Dancer said. “It’s not going to be hard to find work for this piece of equipment, especially after people understand what it’s capable of doing from an end result standpoint.”
The company has also recently replaced single spools of flux-cored wire with the same 400-lb. drums of the FabCOR 86R metal-cored wire for its hand-held MIG operations. The new wire system is paired with Bernard® 400-amp Q-Guns with Centerfire consumables and Miller XMT 456 and Dimension 452 power sources with 70 Series wire feeders.
The Centerfire™ consumables have given Skyline a consistency in its semi-automatic operations that was previously difficult, if not impossible, to attain. With fixed recess tips and a gas diffuser plate built into the nozzle to produce a much calmer gas flow, the Centerfire system reduces common weld defects and variation between operators.
“Sometimes I would walk through the plant and see welds that just didn’t look very good, and I knew it was because our operators had their contact tip sticking out or in too far,” explained Henry. “I always explained that the tip should only be 1/8-in. below the nozzle, but getting everyone to comply with those protocols was another matter. With these Centerfire tips, I can go up to any welder in the shop and their welds will all look exactly the same, and they’re all beautiful.”
Centerfire consumables also feature a unique, drop-in contact tip system that reduces the change out time compared to threaded contact tips that must be screwed into place.
Heavy duty materials and construction also lead to Centerfire consumables lasting up to three times longer, or more in some cases, than other brands of consumables. Companies that can change out their contact tips more quickly and less frequently can realize significant and oftentimes surprising cost savings (see chart).
In all, there are about 35 semi-automatic welding systems running at Skyline. The XMT 456’s provided much needed relief from voltage fluctuations that had been plaguing the company. The unit’s Line Voltage Compensation™ (LVC) feature allows the machine to maintain a steady output power throughout input voltage fluctuations of +/- 10 percent.
Welding carts and overhead booms for the power sources and wire feeders help clean up the shop floor, increasing productivity, material flow and equipment longevity.
“These guys want to work. They get frustrated when they have to go change out wire,” Henry said. “Now they don’t have to change out the wire nearly as often, and with the overhead boom, there aren’t any cables on the floor to roll over. We were welding like it was the 1950’s. Now we’re welding like it’s 2007. That feels good and it makes great business sense.”