Choosing Filler Metal Packaging to Improve Productivity
When a company improves its productivity, it automatically impacts its bottom line—positively. In recent years the emergence of lean manufacturing trends and improved welding processes have supported that goal across many industries. Faster, more efficient workflow simply creates greater throughput. The proper packaging can help reduce downtime for filler metal changeover
and lower labor costs.
Not surprisingly, when a company looks at its overall welding process, power sources are often the top consideration to help improve productivity,and as well they should be. The right power source for the application can make a measurable difference in the speed and quality of welding. So too can the right filler metal—a metal-cored wire process, for example, certainly completes the job faster than a SMAW electrode.But what about the right filler metal (specifically, welding wire) packaging? This too is an important but frequently overlooked aspect of the welding process. Yet choosing and using the right size, style and weight of filler metal packaging, along with implementing good storage practices, can contribute meaningfully to a company’s overall efficiency.
First, the proper filler metal packaging can reduce downtime for changeover—any time spent moving a package off the line, retrieving another and readying it for welding takes away from production. The right package can also help lower labor costs, ensuring that labor is allocated for value-added activities, or those activities that contribute to the overall throughput. Proper storage of packaging further supports good welding wire performance, which in turn can minimize timely and costly rework that takes away from production.Here are a few packaging factors that in conjunction with the right equipment, appropriate welding wire, and good lean manufacturing and fabricating practices can aid in improving a company’s overall productivity. Remember, the impact filler metal packaging has on productivity may not be immediate, but it can make a difference over the course of time.
Less Changeover, Waste = More Arc-On Time Most types of filler metals—for the sake of this discussion, welding wires (solid, flux-cored and metal-cored)—are available in a variety of styles and weights. Most range from as small as 15-lb. spools to as large as 60-lb coils and 900 or 1000-lb. drums. The first consideration when choosing the right packaging is whether the welding operation is inside or outside. For outside construction, shipbuilding or general field welding applications, portability is key in maintaining good productivity; dragging a large filler metal package around is simply not feasible. It takes too much time and labor. Instead a 15-lb. spool would be appropriate.
In a one to two man (indoor) shop where the weekly volume of welding wire usage falls into the 150 to 200-lb. range, 33-lb. spools can help minimize changeover (as compared to a 15-lb. spool, for example) and would be appropriate to the volume of products welded. Conversely, a 15-person shop that currently uses 33-lb. spools would in all likelihood use these spools in one day. Moving to 60-lb. coils here could minimize the changeover to once every two days and allow for more arc-on time.
These situations are relatively straightforward: use smaller package for smaller volume production and increase incrementally according to the number of welding operators to minimize downtime for changeover and aid in greater productivity. When a welding operation reaches a higher volume with more welding operators (or an automated system) and a greater desired throughput, however, choosing the right packaging becomes a little more complicated. Fortunately, the option to minimize downtime and costs, and improve productivity by going to a larger package usually becomes more practical.
For instance, a company that employs robotics or hard fixture automation in their facility would obviously require a greater volume of welding wire in a larger package to meet its production goals than a 15-man shop. How large is the question.
In many cases, 400-lb. or 600-lb. drums work well in high volume, automated welding operations. Consider a company that uses a million pounds of welding wire per year paid out in 400-lb. drums. They would require approximately 208 changes per month, or about 2496 changes in a year. At an average of 30 minutes per changeover, that company could spend just about 104 hours of its labor per month changing out the drums. Here, moving to a larger weight drum might make sense; instead of using those 104 hours for changeover, a larger drum could allow a portion of that time (some will still be required for changeover) to be used toward meeting greater production goals.
Here’s how: a 900-lb. drum takes the same 30 minutes to changeover, but requires only about 93 changes per month (1116 per year), for a total monthly changeover labor of 46.5 hours. Subtracted from the previous 104 hours of changeover per 400-lb. drum, that adds up to a savings of 57.5 hours per month of labor, or approximately 690 hours saved per year. These hours can then be reallocated to additional welding and/or other parts of the welding process (cleaning, fixturing, etc) that instead assist in productivity increases.
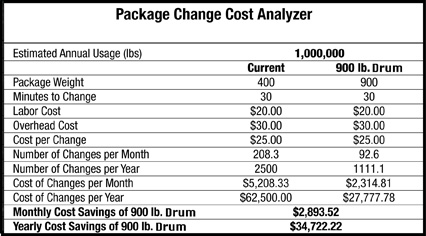
savings.
Finally, the right weight package can also minimize labor spent taking care of waste—labor that can again be spent elsewhere to contribute to the company’s productivity. Some filler metal drums are now 100 percent recyclable, which minimizes additional downtime for separating metal and fiber parts into the appropriate waste containers and it also lowers the cost of that waste disposal. Not to mention, recyclable drums are safer; they reduce the risk of injuries caused by cutting away the metal chimes. Steel reels that are often used to hold solid wires can also be scrapped for recycling, again minimizing labor for waste disposal that could instead be used in the weld cell.
Stay Close, Follow the Rules
Where and how a company places its filler metal package, while it is in use or in storage, can also contribute to the overall efficiency and productivity of its welding operation.
The package, whether a spool, reel or drum, needs to easily fit into the allotted footprint in a weld cell lest extra time be spent trying to maneuver it into the space. Ideally, it should take up as little space as possible. In high-volume production facilities, placing two drums on a mezzanine, for example, may be the most appropriate space and the easiest to aid in good work flow, another factor that contributes to improved productivity. When one drum is empty, the spare one can be engaged and the next spare can be added during a non-production time.
The filler metal package should also be in a place where it is not in the way of moving equipment, such as forklifts, that can damage it. Damaged packages can cause unnecessary downtime for change-out, and this damage can also void the warranties provided by filler metal manufacturers. Not only does a company run the risk of downtime and labor for replacing the package, but it could also incur additional cost for new wires. Drums, spools and reels should not be double-stacked for the same reason. Stacking can damage the wire, and it can also be dangerous to welding operators should the reel or drum fall.
Companies should work with a filler metal manufacturer or welding distributor to ensure timely delivery of welding wire to a designated location. There should always be enough packages of filler metal in storage to prevent a cease in production. Also, companies should be certain to rotate stock so as to ensure that no packaging sits in storage for an extended period of time; those filler metals delivered first should be used first to gain the best welding performance.
Upon arrival, the filler metal package should be placed in an area that is easily accessible when changeover is necessary. Excessive downtime can occur if a welding operator has to go a far distance to acquire another package and that again takes valuable time away from the weld cell.
Likewise, proper storage of filler metal packages help ensure top performance from the filler metal and can help companies avoid unnecessary rework—welding operators can contribute to a product’s throughput rather than spend time repairing mistakes. As a rule, until the package is opened it should be stored in a dry, well-ventilated environment to prevent moisture damage, the number one culprit of welding wire damage. Additional storage information recommended by the filler metal manufacturer should always be followed.
Make an Assessment
Packaging may be an easily overlooked area of the welding operation, but it can positively contribute to a company’s overall efficiency. Companies that experience excessive downtime for package changeover, have high waste disposal costs or increased labor for package disposal, or those that simply are looking to increase throughput and their bottom line may want to look at their current packaging. Filler metal manufacturers or a trusted welding distributor can provide audits to help companies determine which is the best option—in addition to the right equipment and welding wire—to help improve workflow and increase productivity.