Understanding, Storing and Handling Filler Metals: Ways You Can Gain Top Welding Performance and Reduce Costs
Whether you are in the shop or the field, or if you weld a little or a lot, taking proper care of your filler metals is crucial to achieving good weld quality and avoiding additional downtime for equipment maintenance and repairs. Filler metals (including stick electrodes and solid or flux-cored wires) that become damaged, either by moisture or contaminants, cause poor weld quality that ultimately can increase your costs. Not only do you need to dispose of damaged filler metals, but you also void the warranty on your products if you do not follow proper procedures for storage and handling them. Plus, you add to your costs for purchasing new filler metals and to your downtime for replacing them.
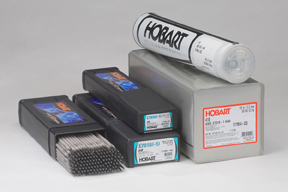
consistent welding performance and reduce costs.
When manufacturers package their filler metals, the products have been carefully sealed to ensure that they are in the best possible condition. Regardless of the state of your shop or the environment to which you expose them in the field, it is important for you to keep them that way. Here are some tips for properly storing and handling your filler metals so that you achieve the best performance and keep your costs low.
Stick Electrodes: What You Don’t Know Can Hurt Your Welding Performance
Stick electrodes are a common filler metal choice for equipment repairs that occur in the field, as they are lightweight and do not require a shielding gas. They are also available in a variety of alloys, making them usable on many types of materials. Stick electrodes are best suited for smaller repairs due to the need for frequent electrode change out.
Moisture, in particular, is the biggest enemy of stick electrodes. Not only can it cause porosity and hydrogen-induced cracking, but also it can result in costly downtime for rework associated with these defects.
Never leave a can or carton of stick electrodes open in the shop or in the field, especially if you are using a low-hydrogen product. Instead, you should store your stick electrodes as recommended by the manufacturer, which may require the product to be placed in a storage oven designed for this purpose. Filler manufacturers provide recommendations for the best storage temperature for each of their products. For example, a stick electrode classified as American Welding Society (AWS) E7018-1 H4R (a commonly designated low-hydrogen product) may have a storage temperature of 220- to 350-degrees Fahrenheit. This temperature keeps the stick electrode at its optimum operating condition and also ensures it provides the low-hydrogen weld deposit indicated by its AWS classification — in this case, 4 ml. per 100 grams (indicated by the H4). Check with your filler metal manufacturer for proper storage temperatures for your stick electrodes or consult the original package for information.
When possible, select stick electrode packages that offer good moisture resistance. Options include wax coated cartons or resealable plastic packages. Remember to close the package after you retrieve your stick electrode. Also note, for critical repairs, such as those involving a load-bearing joint, you may have specific welding procedures or codes that require you to discard your stick electrodes after a given period of time—regardless of the type of package you have or if you’ve stored it properly in an oven.
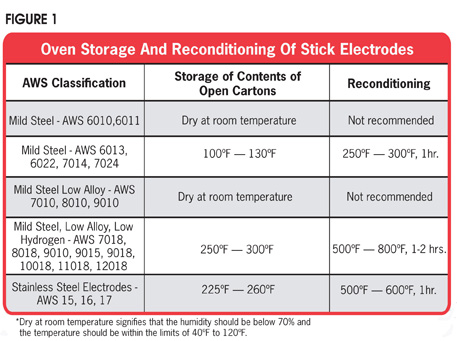
Most filler metal manufacturers offer information on the original packaging for reconditioning stick electrodes should they become exposed to moisture (see Figure 1 for examples). Reconditioning involves placing the exposed stick electrodes in an oven at a given temperature for a specified period of time. In the example of the AWS E7018-1 H4R stick electrode, this product might have a reconditioning recommendation of one hour at 575 degrees Fahrenheit. Again, be certain to check your particular stick electrode package, or call the manufacturer for the proper reconditioning information.
From Solid Wire to Flux-Cored: Your Options and How to Handle Them
There are three options for welding wires to use on your equipment repairs: solid wires and gas-shielded or self-shielded flux-cored wires. Metal-cored wires are also available, but these tend to be slightly more expensive and are typically used for repairs on larger heavy equipment.
Solid wires, as their name implies, are solid throughout their entire cross section. Many welders choose solid wires because of they offer higher efficiency than stick electrodes and because they are versatile for welding on a wide range of materials. They are also easier for less experienced welders to use. These wires require an external shielding gas, so if you are using them in the field, you should consider using a windshield to prevent shielding gas from blowing away from the arc and weld puddle.
Flux-cored wires are available in two varieties: gas-shielded and self-shielded. Gas-shielded flux-cored wires are good for welding on thicker parts or in out-of-position applications, as they have a flux coating that solidifies rather quickly to help control the weld puddle. They require an external shielding gas and are usually used in shop applications. Self-shielded flux-cored wires do not require external shielding gas. Instead, the flux from the wire creates a shielding environment that protects the arc from the atmosphere as the wire burns. Both type of wires generate slag, which you need to remove after completing your weld and/or in between weld passes on a multi-pass application.
Regardless of which welding wire you select, always wear gloves when handling them to prevent moisture from your hands damaging the wire. Moisture causes rust to form on the surface of the wire (particularly solid wires), which can cause porosity or poor wire feeding. Note, you cannot recondition welding wires should they become damaged by moisture.
Also, keep your welding wires away from water, grease, oil and debris, as these contaminants can all cause poor welding performance and weld quality that will ultimately affect your productivity and costs. And, if you often use an oxy-fuel torch for cutting or if you carbon arc gouge prior to welding, keep these activities away from where you are storing your welding wires or where you are welding. Dust from these processes can accumulate on the wires, causing poor wire feeding or clogging your contact tip and nozzle, which leads to an erratic arc. You may want to consider an enclosed wire feeder to help protect against such contaminants, but remember that this type of feeder is no replacement for proper handling or storage practices.
There are two main ways to store your welding wires when you are not using them. The best practice is to remove the spool from the wire feeder, place it in a clean plastic bag and close it securely. Next, place the secured package into the original box and store it in a clean dry area until you are ready to use it again. If you are not able to take these steps, the least you should do is cover the welding wire spool securely with a plastic bag while it is on the feeder. Remember, however, that with either practice there are limits to how long you can store an open package of welding wire. Contact your filler metal manufacturer for details.